Welches Schutzgas beim WIG- und welches beim MIG/MAG-Schweißen?
WIG-Schutzgas
Wie aus dem Namen des Verfahrens schon abgeleitet werden kann, werden in der Regel inerte Gase zum WIG-Schweißen eingesetzt. Schutzgase sind in DIN EN 439 genormt. Diese tragen nach Norm die Bezeichnungen l1, l2 und l3.
Das am häufigsten beim WIG-Schweißen verwendete Schutzgas ist Argon (l1). Der Reinheitsgrad sollte mindestens 99,95% betragen. Bei Metallen, die eine sehr gute Wärmeleitfähigkeit haben, wie Aluminium oder Kupfer, kommt aber auch Helium (l2) zum Einsatz. Unter Helium als Schutzgas ist der Lichtbogen heißer. Vor allem aber ist die Wärmeverteilung zwischen dem Kern und dem Rand des Lichtbogens gleichmäßiger. Der Einsatz von reinem Helium beim WIG-Schweißen ist selten und auf Sonderfälle beschränkt, dagegen kommen Argon/Helium-Gemische (l3) mit 25, 50 oder 75% Helium seit einigen Jahren vermehrt zur Verwendung. Damit kann z.B. bei dickeren Aluminiumstrukturen die zur Erreichung eines ausreichenden Einbrandes erforderliche Vorwärmtemperatur verringert werden. Vielfach ist auch eine Erhöhung der Schweißgeschwindigkeit möglich. Beim WIG-Schweißen von nichtrostenden Chrom-Nickel-Stählen werden zu diesem Zweck auch Argon / Wasserstoffgemische (R1) eingesetzt, jedoch sollte der Wasserstoffgehalt aus Gründen der Porenvermeidung nicht wesentlich über 5% liegen.
Die Schutzgasdurchflußmenge richtet sich nach dem Gasdüsendurchmesser und der umgebenden Luftströmung. Als Richtwert kann bei Argon von einem Volumenstrom von 5-10 I / min ausgegangen werden. In zugigen Räumen Bild 4 sind u. U. größere Durchflußmengen erforderlich. Bei Argon / Helium-Gemischen müssen wegen der geringeren Dichte von Helium höhere Durchflußmengen eingestellt werden.
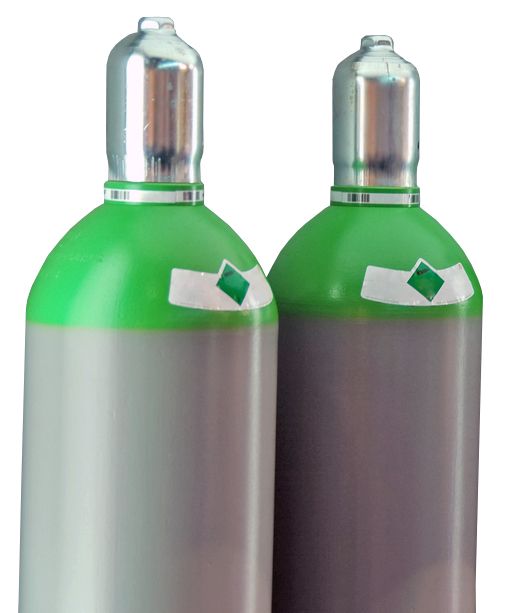
MIG/MAG-Schutzgas
Schutzgase zum MIG/MAG-Schweißen findet man in DIN EN 439. In dieser Norm sind alle Schutzgase zum Lichtbogenschweißen und -schneiden genormt. Die Schutzgase werden in sieben Gruppen und in weitere Untergruppen unterteilt.
Übersicht über die Gruppen der Schutzgase
Die Gruppe R
Die Gruppe R enthält Argon / Wasserstoff-Gemische, die eine reduzierende Wirkung haben. Die Gase der Gruppe R1 finden neben Argon und Helium Anwendung zum WIG-Schweißen und zum Plasmaschweißen, die Gase der Untergruppe 2 mit höherem Wasserstoffgehalt(H) dagegen zum Plasmaschneiden und zum Wurzelschutz (Formiergase).
Die Gruppe I
In der Gruppe I sind die inerten Gase zusammengefasst. Hier findet man Argon(Ar) und Helium (He) sowie Argon/Helium-Gemische. Sie werden zum WIG-, MIG-, und Plasmaschweißen eingesetzt, sowie auch zum Wurzelschutz.
Die Gruppe M
In der großen M-Gruppe, die noch in M1,M2 und M3 unterteilt ist, sind die Mischgase zum MAG-Schweißen zusammengefasst. Auch hier gibt es in jeder Gruppe noch 3 bzw. 4 Untergruppen. Die Gase sind von M1.1 bis M3.3 nach Ihrem Oxidationsverhalten geordnet, d.h. M1.1 verhält sich schwach oxidierend, M3.3 ist am stärksten oxidierend. Hauptbestandteil dieser Gase ist Argon, an aktiven Komponenten sind Sauerstoff (O) oder Kohlendioxid (CO2) bzw. Sauerstoff und Kohlendioxid (Dreikomponenten-Gase) zugemischt.
Die Gruppe C
In der Reihe der Gase zum MAG-Schweißen folgt in der Gruppe C das reine Kohlendioxid und ein Kohlendioxid /Sauerstoffgemisch. Letzteres hat allerdings in Deutschland keine Bedeutung. Die Gase der Gruppe C sind am stärksten oxidierend, weil das CO2 bei der hohen Temperatur des Lichtbogens zerfällt, wobei neben Kohlenmonoxid auch große Mengen Sauerstoff entstehen.
Die Gruppe F
In der Gruppe F findet man schließlich Stickstoff (N) und ein Stickstoff / Wasserstoff-Gemisch. Beide Gase können zum Plasmaschneiden und zum Formieren verwendet werden.
Neben dem Oxidationsverhalten verändern sich mit der Zusammensetzung des Gases auch die elektrischen und die physikalischen Eigenschaften im Lichtbogenraum und damit die Schweißeigenschaften. Durch den Zusatz von Helium zum Argon verbessert sich z.B. die Wärmeleitfähigkeit und der Wärmeinhalt der Lichtbogenatmosphäre. Beides führt zu einem energiereicheren Lichtbogen und damit zu einem besseren Einbrandverhalten. Das Zumischen von aktiven Komponenten bei den Mischgasen führt u.a. zu einer feineren Tropfenbildung beim Abschmelzen der Drahtelektrode. Ferner wird der Wärmetransport im Lichtbogen verbessert. Auch hieraus resultiert ein besseres Einbrandverhalten.
Die benötigte Durchflussmenge des Schutzgases lässt sich mit einer Faustregel errechnen, und zwar soll sie 10 - 12 x Drahtdurchmesser in Liter/Minute sein.
Beim MIG-Schweißen von Aluminium werden, wegen der großen Oxidationsneigung des Werkstoffs, etwas darüberhinausgehende Durchflussmengen eingestellt, bei Ar / He- Mischgasen, wegen der geringen Dichte von Helium, auch wesentlich höhere. Das aus der Flasche oder der Ringleitung kommende Gas wird zunächst im Druck reduziert. Die eingestellte Durchflussmenge kann an einem Manometer, das zusammen mit einer Staudüse geeicht ist, abgelesen werden, oder an einem Durchflussmengenmesser mit Schwebekörper.
Bezeichnung |
Angaben in Volumenprozent (Vol %) |
Übliche |
Bemerkungen |
||||||
Gruppe |
Kennzahl |
oxidierend |
inert |
reduziert |
reaktionsträge |
|
|
||
|
|
CO2 |
O2 |
Ar |
He |
H2 |
N2 |
||
R |
1 |
|
|
Rest² |
|
> 0 bis 15 |
|
WIG, Plasmaschweißen, Plasmaschneiden, Wurzelschutz |
|
2 |
|
|
Rest² |
|
> 15 bis 35 |
|
|||
I |
1 |
|
|
100 |
|
|
|
MIG, WIG, Plasmaschweißen, Wurzelschutz |
inert |
2 |
|
|
|
100 |
|
|
|||
3 |
|
|
Rest² |
> 0 bis 95 |
|
|
|||
M1 |
1 |
> 0 bis 5 |
|
Rest² |
|
> 0 bis 5 |
|
MAG |
schwach oxidierend |
2 |
> 0 bis 5 |
|
Rest² |
|
|
|
|||
3 |
|
> 0 bis 3 |
Rest² |
|
|
|
|||
4 |
> 0 bis 25 |
> 0 bis 3 |
Rest² |
|
|
|
|||
M2 |
1 |
> 0 bis 25 |
|
Rest² |
|
|
|
|
|
2 |
|
> 3 bis 10 |
Rest² |
|
|
|
|||
3 |
> 0 bis 5 |
> 3 bis 11 |
Rest² |
|
|
|
|||
4 |
> 0 bis 25 |
> 0 bis 8 |
Rest² |
|
|
|
|||
M3 |
1 |
> 25 bis 50 |
|
Rest² |
|
|
|
|
|
2 |
|
> 10 bis 15 |
Rest² |
|
|
|
|||
3 |
>5 bis 50 |
> 8 bis 15 |
Rest² |
|
|
|
|||
C |
1 |
100 |
|
|
|
|
|
stark oxidierend |
|
2 |
Rest |
> 0 bis 30 |
|
|
|
|
|||
F |
1 |
|
|
|
|
|
100 |
Plasmaschneiden, Wurzelschutz |
reaktionsträge |
2 |
|
|
|
|
> 0 bis 50 |
Rest |
reduzierend |
Einteilung der Schutzgase für Lichtbogenschweißen und -schneiden