E-Hand (MMA) Grundlagen
- Allgemeines zum E-Hand-Schweißen
- Stromart
- Elektrodentyp
- Eigenschaften der Umhüllungstypen
- Richtig E-Hand Schweißen
- Zünden des Lichtbogens
- Führen der Elektrode
- Magnetische Blaswirkung
- Schweißparameter
- Stromstärken in Abhängigkeit vom Elektrodendurchmesser
- Benötigete Ausrüstung
Allgemeines
Das E-Hand-Schweißen (Prozessnummer 111) zählt zu den Schmelzschweißverfahren und noch näher zugeordnet zu den Metall-Lichtbogenschweißverfahren. ISO 857-1 (Ausgabe 1998) erklärt die Schweißprozesse dieser Gruppe aus dem Englischen übersetzt wie folgt:
Metall-Lichtbogenschweißen: Lichtbogenschweißprozess unter Benutzung einer verbrauchenden Elektrode. Metall-Lichtbogenschweißen ohne Gasschutz: Metall-Lichtbogenschweißprozess ohne extern zugegebenes Schutzgas und Manuelles Metall-Lichtbogenschweißen: Von Hand ausgeführtes Metall- Lichtbogenschweißen unter Benutzung einer umhüllten Elektrode.
In Deutschland nennen wir das zuletzt genannte Verfahren Lichtbogenhandschweißen oder kurz E-Hand-Schweißen (umgangssprachlich auch Elektrodeschweißen). Im englischen Sprachraum ist es unter der Abkürzung MMA oder MMAW (Manual Metal Arc Welding) bekannt. Es ist dadurch gekennzeichnet, dass der Lichtbogen zwischen einer abschmelzenden Elektrode und dem Schmelzbad brennt. Es gibt keinen externen Schutz, jegliche Schutzwirkung vor der Atmosphäre geht von der Elektrode aus. Die Elektrode ist dabei Lichtbogenträger und Schweißzusatz. Die Umhüllung bildet Schlacke und/oder Schutzgas welche u.a. den übergehenden Tropfen und das Schmelzbad vor dem Zutritt der atmosphärischen Gase Sauerstoff, Stickstoff und Wasserstoff schützen.
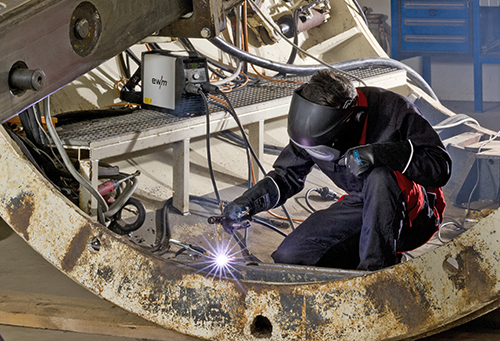
Stromart
Zum Lichtbogenhandschweißen (E-Hand-Schweißen) kann im Prinzip sowohl Gleichstrom, als auch Wechselstrom eingesetzt werden, jedoch lassen sich nicht alle Umhüllungstypen der Stabelektroden an sinusförmigem Wechselstrom verschweißen, z.B. nicht die reinbasischen Elektroden. Beim Schweißen an Gleichstrom wird bei den meisten Elektrodentypen der Minuspol an die Elektrode und der Pluspol ans Werkstück angeschlossen. Eine Ausnahme machen auch hier die basischen Elektroden. Sie lassen sich besser am Pluspol verschweißen. Das Gleiche gilt für bestimmte Fabrikate von Zelluloseelektroden. Näheres dazu kann im Abschnitt Elektrodentypen nachgelesen werden. Die Elektrode ist das Werkzeug des Schweißers. Er führt den an ihr brennenden Lichtbogen in der Schweißfuge und schmilzt dabei die Fugenkanten auf Bild 2. Je nach Fugenart und Grundwerkstoffdicke sind dafür unterschiedliche Stromstärken erforderlich. Da die Strombelastbarkeit der Elektroden, abhängig von ihrem Durchmesser und ihrer Länge begrenzt ist, sind die Stabelektroden in verschiedenen Durchmessern und Längen lieferbar. Tabelle 1 zeigt die in DIN EN 759 genormten Abmessungen. Mit zunehmendem Kernstabdurchmesser können höhere Schweißströme angewendet werden.
Elektrodentypen
Es gibt Stabelektroden mit sehr unterschiedlich zusammengesetzten Umhüllungen. Der Aufbau der Umhüllung bestimmt den Abschmelzcharakter der Elektrode, ihre Schweißeigenschaften und die Gütewerte des Schweißgutes (genauere Informationen im Abschnitt "Welche Elektrode für welchen Zweck" . Nach DIN EN 499 gibt es bei Stabelektroden zum Schweißen von unlegierten Stählen unterschiedliche aufgeführten Umhüllungstypen. Dabei muss unterschieden werden zwischen Grundtypen und Mischtypen. Die verwendeten Buchstaben für die Bezeichnung stammen von den englischen Begriffen her. Hier bedeutet C=cellulose (Zellulose), A=acid (sauer), R=rutile (Rutil) und B=basic (basisch). In Deutschland spielt der Rutiltyp eine dominierende Rolle. Stabelektroden können dünnumhüllt sein, mitteldickumhüllt oder dickumhüllt. Bei den Rutilelektroden, die in allen drei Umhüllungsdicken üblich sind, werden deshalb die dickumhüllten Elektroden zur besseren Unterscheidung mit RR bezeichnet. Bei legierten und hochlegierten Stabelektroden kommt diese Vielfalt von Umhüllungstypen nicht vor. Bei den Stabelektroden zum Schweißen nichtrostender Stähle, die in DIN EN 1600 genormt sind, unterscheidet man z.B. nur zwischen Rutilelektroden und basischen Typen, ebenso bei Stabelektroden zum Schweißen warmfester Stähle (DIN EN 1599), jedoch gibt es auch hier bei den Rutilelektroden rutil-basische Mischtypen, ohne dass dies besonders ausgewiesen wird. Dies ist z. B. der Fall bei Elektroden, die bessere Schweißeigenschaften in Zwangslagen haben. Stabelektroden zum Schweißen hochfester Stähle (DIN EN 757) gibt es nur mit basischer Umhüllung.
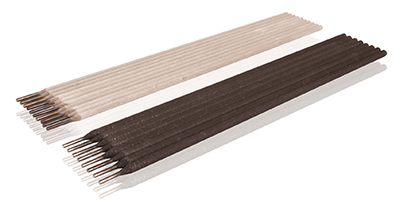
Eigenschaften der Umhüllungstypen
Die Zusammensetzung und die Dicke der Umhüllung beeinflusst in besonderem Maße die Schweißeigenschaften. Dies bezieht sich sowohl auf die Stabilität des Lichtbogens, als auch auf den Werkstoffübergang beim Schweißen und die Viskosität von Schlacke und Schmelzbad. Besonders die Größe der im Lichtbogen übergehenden Tropfen ist dabei von Bedeutung.
Das Bild zeigt schematisch den Tropfenübergang der vier Grundtypen von Umhüllungen: Zellulose (a), Rutil (b), Sauer (c), Basisch (d).
Die Umhüllung besteht überwiegend aus organischen Bestandteilen, die im Lichtbogen verbrennen und dabei Schutzgas zum Schutz der Schweißstelle bilden. Da die Umhüllung außer Zellulose und anderen organischen Stoffen nur geringe Mengen von lichtbogenstabilisierenden Stoffen enthält, entsteht kaum Schlacke. Zellulosetypen sind besonders gut für Fallnahtschweißungen geeignet, weil kein Schlackenvorlauf zu befürchten ist.
Der saure Typ (A), dessen Umhüllung zum größten Teil aus Eisen- und Manganerzen besteht, bietet der Lichtbogenatmosphäre größere Mengen Sauerstoff an. Dieser wird auch vom Schweißgut aufgenommen und verringert dadurch dessen Oberflächenspannung. Die Folge sind ein sehr feiner, sprühregenartiger Werkstoffübergang und ein dünnflüssiges Schweißgut. Elektroden diesen Typs sind deshalb nicht für das Schweißen in Zwangslagen geeignet. Der Lichtbogen ist auch sehr „heißgehend“, gestattet zwar hohe Schweißgeschwindigkeiten, neigt aber zur Bildung von Einbrandkerben. Die beschriebenen Nachteile haben dazu geführt, dass Stabelektroden des reinen sauren Typs in Deutschland kaum noch angewendet werden.
An ihre Stelle ist der rutilsaure Typ (RA) getreten, ein Mischtyp zwischen der sauren und der Rutilelektrode. Die Elektrode hat auch dementsprechende Schweißeigenschaften Die Umhüllung des Rutiltyps (R/RR) besteht zum größten Teil aus Titandioxid in Form der Mineralien Rutil (TiO2) oder Ilmenit (TiO2 . FeO) oder auch von künstlichem Titandioxid. Die Elektroden dieses Typs zeichnen sich aus durch einen fein bis mitteltropfigen Werkstoffübergang, ein ruhiges, spritzerarmes Abschmelzen, eine sehr feine Nahtzeichnung, eine gute Schlackenentfernbarkeit und ein gutes Wiederzündverhalten. Letzteres ist in dieser Form nur bei Rutilelektroden mit hohem Anteil von TiO2 in der Umhüllung zu beobachten. Es bedeutet, dass bei einer bereits einmal angeschmolzenen Elektrode ein Wiederzünden ohne Entfernen des Hüllenkraters möglich ist. Der im Krater gebildete Schlackenfilm hat bei ausreichend hohem TiO2-Gehalt fast eine Leitfähigkeit wie ein Halbleiter, so dass beim Aufsetzen des Kraterrandes auf das Werkstück soviel Strom fließt, dass der Lichtbogen zünden kann, ohne das der Kernstab das Werkstück berührt. Ein solches spontanes Wiederzünden ist immer dann wichtig, wenn der Schweißvorgang, z.B. bei kurzen Nähten, häufig unterbrochen wird.
Neben dem reinen Rutiltyp gibt es bei dieser Gruppe von Elektroden noch einige Mischtypen. Da ist der Rutil-Zellulose- Typ (RC) zu nennen, bei dem ein Teil des Rutils durch Zellulose ersetzt wurde. Da Zellulose beim Schweißen verbrennt, bildet sich weniger Schlacke. Dieser Typ kann deshalb auch in Fallnaht (Pos. PG) verschweißt werden. Er besitzt aber auch gute Schweißeigenschaften in den meisten anderen Positionen.
Ein weiterer Mischtyp ist der rutilbasiche Typ (RB). Er ist etwas dünner umhüllt, als der RR-Typ. Dies und die besondere Schlackencharakteristik macht ihn besonders geeignet zum Schweißen in senkrecht- steigender Position (PF). Bliebe noch der basische Typ (B). Hierbei besteht die Umhüllung zum größten Teil aus den basischen Oxiden des Calziums (CaO) und des Magnesiums (MgO), denen als Schlackenverdünner Flußspat (CaF2) zugegeben wird. Der Flussspat verschlechtert in höheren Gehalten die Wechselstromschweißbarkeit. Reinbasische Elektroden sind deshalb an sinusförmigem Wechselstrom nicht zu verschweißen, jedoch gibt es auch Mischtypen mit weniger Flussspat in der Umhüllung, die an dieser Stromart verwendbar sind. Der Werkstoffübergang der basischen Elektroden ist mittel- bis grobtropfig und das Schmelzbad zähfließend. Die Elektrode ist in allen Positionen gut verschweißbar. Die entstehenden Raupen sind aber wegen der größeren Viskosität des Schweißgutes etwas überwölbt und grober gefiedert. Das Schweißgut hat sehr gute Zähigkeitseigenschaften.
Basische Umhüllungen sind hygroskopisch. Auf besonders sorgfältige, trockene Lagerung der Elektroden ist deshalb zu achten. Feucht gewordene Elektroden müssen rückgetrocknet werden. Das Schweißgut besitzt aber, wenn die Elektroden trocken verschweißt werden, einen sehr niedrigen Wasserstoffgehalt. Neben Stabelektroden mit normalem Ausbringen (<105%) gibt es auch solche, die durch Eisenpulver, das über die Umhüllung zugegeben wird, ein höheres Ausbringen haben, meist >160%. Solche Elektroden werden Eisenpulvertypen oder auch Hochleistungselektroden genannt. Durch ihre große Abschmelzleistung sind sie für viele Anwendungen wirtschaftlicher einzusetzen als Normalelektroden, jedoch ist ihre Anwendung in der Regel auf die waagerechte (PA) und die horizontale Position (PB) beschränkt.
Richtig E-Hand-Schweißen
Der Schweißer benötigt eine gute Ausbildung, und zwar nicht nur in handwerklicher Hinsicht, sondern er muss auch über entsprechendes fachkundiges Wissen verfügen, um Fehler zu vermeiden. Die Ausbildungsrichtlinien des DVS – Deutscher Verband für Schweißen und verwandte Verfahren e.V. sind weltweit anerkannt und wurden inzwischen auch vom Internationalen Schweißverband (IIW) übernommen. Vor dem Beginn des Schweißens werden die Werkstücke in der Regel geheftet. Die Heftstellen müssen so lang und dick ausgeführt werden, dass die Werkstücke sich beim Schweißen nicht unzulässig stark zusammenziehen können und die Heftstellen nicht reißen.
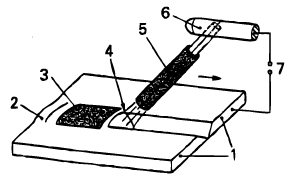
- Werkstück
- Schweißnaht
- Schlacke
- Lichtbogen
- Umhüllte Elektrode
- Elektrodenhalter
- Schweißstromquelle
Zünden des Lichtbogens
Der Schweißprozess wird beim E-Hand- Schweißen durch eine Kontaktzündung eingeleitet. Um den Stromkreis zu schließen muss zunächst zwischen Elektrode und Werkstück ein Kurzschluss erzeugt und die Elektrode sofort danach leicht angehoben werden – der Lichtbogen zündet. Der Zündvorgang sollte nie außerhalb der Fuge erfolgen, sondern grundsätzlich an solchen Stellen, die nach dem Brennen des Lichtbogens sofort wieder aufgeschmolzen werden. An Zündstellen, an denen dies nicht geschieht, können nämlich bei entsprechend empfindlichen Werkstoffen durch die plötzliche Erwärmung Risse entstehen. Bei basischen Elektroden, die zu Ansatzporosität neigen, muss das Zünden sogar deutlich vor dem eigentlichen Schweißanfang erfolgen. Danach wird der Lichtbogen zum Anfangspunkt der Naht zurückgeführt und im weiteren Verlauf des Schweißens werden die ersten abgesetzten Tropfen, die meist porös sind, wieder aufgeschmolzen.
Führen der Elektrode
Die Elektrode wird zur Blechoberfläche senkrecht oder leicht schräg angestellt. Sie wird leicht in Schweißrichtung geneigt. Die sichtbare Lichtbogenlänge, d.h. der Abstand zwischen Kraterrand und Werkstückoberfläche soll dabei etwa dem Kernstabdurchmesser entsprechen. Basische Elektroden müssen mit sehr kurzem Lichtbogen verschweißt werden (Abstand=0,5 x Kernstabdurchmesser). Um dies zu gewährleisten, müssen sie steiler geführt werden als Rutilelektroden. In den meisten Positionen werden Strichraupen geschweißt oder es wird mit nach oben hin größer werdender Fugenbreite leicht gependelt. Nur in der Position PF werden Pendelraupen in der ganzen Breite der Fuge gezogen. In der Regel wird schleppend geschweißt, nur in der Position PF wird die Elektrode stechend angestellt.
- Schweißfuge
- Stabelektrode
- Flüssiges Schweißgut
- Flüssige Schlacke
- Erstarrte Schlacke
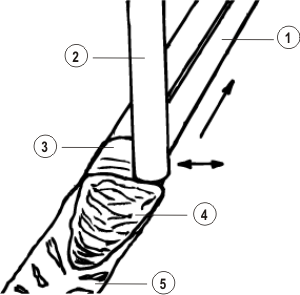
Magnetische Blaswirkung
Unter Blaswirkung versteht man eine Erscheinung, bei welcher der Lichtbogen durch Ablenkung aus seiner Mittelachse verlängert wird und dabei ein zischendes Geräusch von sich gibt. Durch diese Ablenkung können Ungänzen entstehen. So kann der Einbrand unzulänglich werden und bei schlackenführenden Schweißprozessen können durch Schlackenvorlauf in der Naht Schlackeneinschlüsse entstehen. Die Ablenkung erfolgt durch Kräfte, die aus dem umgebenden Magnetfeld herrühren. Wie jeder stromdurchflossene Leiter sind auch Elektrode und Lichtbogen von einem ringförmigen Magnetfeld umgeben – dieses wird im Bereich des Lichtbogens beim Übergang in den Grundwerkstoff umgelenkt. Dadurch werden die magnetischen Kraftlinien an der Innenseite verdichtet und an der Außenseite erweitert. Der Lichtbogen weicht in das Gebiet verminderter Flussliniendichte aus. Dabei verlängert er sich und gibt wegen der nun erhöhten Lichtbogenspannung ein zischendes Geräusch von sich. Der Gegenpol übt also eine abstoßende Wirkung auf den Lichtbogen aus. Eine andere magnetische Kraft rührt daher, dass das Magnetfeld sich in einem ferromagnetischen Werkstoff besser ausbreiten kann, als in Luft. Der Lichtbogen wird deshalb von großen Eisenmassen angezogen. Dies zeigt sich z.B. auch dadurch, dass er beim Schweißen auf einem magnetisierbaren Werkstoff an den Blechenden nach Innen abgelenkt wird. Der Ablenkung des Lichtbogens kann man durch entsprechende Schrägstellung der Elektrode begegnen. Da die Blaswirkung beim Schweißen mit Gleichstrom besonders groß ist, kann man sie, wo dies möglich ist, durch das Schweißen an Wechselstrom vermeiden oder zumindest erheblich vermindern. Besonders stark kann die Blaswirkung wegen der umgebenden Eisenmassen beim Schweißen von Wurzellagen werden. Hier hilft es, wenn man den Magnetfluss durch eng beieinander liegende, nicht zu kurze Heftstellen, unterstützt.
Schweißparameter
Beim E-Hand-Schweißen wird nur die Stromstärke eingestellt, die Lichtbogenspannung ergibt sich aus der Lichtbogenlänge, die der Schweißer einhält. Bei der Einstellung der Stromstärke muss die Strombelastbarkeit des verwendeten Elektrodendurchmessers berücksichtigt werden. Dabei gilt die Regel, dass die unteren Grenzwerte für das Schweißen von Wurzellagen und für die Position PF gelten, die oberen dagegen für die übrigen Positionen und für Füll- und Decklagen. Mit zunehmender Stromstärke steigt die Abschmelzleistung und die damit in Zusammenhang stehende Schweißgeschwindigkeit. Auch der Einbrand nimmt mit steigendem Strom zu. Die angegebenen Stromstärken gelten nur für un- und niedriglegierte Stähle. Bei hochlegierten Stählen und Nickelbasiswerkstoffen müssen wegen des größeren elektrischen Widerstandes des Kernstabes niedrigere Werte eingestellt werden.
Stromstärken in Abhängigkeit vom Elektrodendurchmesser
Folgende Faustregeln zur Berechnung der einzelnen Stromstärken in A müssen Sie beachten:
20-40 x Ø
- Bei einem Durchmesser von 2,0 mm sollte die Stromstärke zwischen 40-80 A liegen
- Bei einem Durchmesser von 2,5 mm sollte die Stromstärke zwischen 50-100 A liegen
30-50 x Ø
- Bei einem Durchmesser von 3,2 mm sollte die Stromstärke zwischen 90-150 A liegen
- Bei einem Durchmesser von 4,0 mm sollte die Stromstärke zwischen 120-200 A liegen
- Bei einem Durchmesser von 5,0 mm sollte die Stromstärke zwischen 180-270 A liegen
35-60 x Ø
- Bei einem Durchmesser von 6,0 mm sollte die Stromstärke zwischen 220-360 A liegen
Zum erfolgreichen E-Hand-Schweißen benötigen Sie die nachstehende Ausrüstung:
- Schweißstromquelle
- Elektrodenhalter
- Stabelektrode
- Werkstückklemme / Massezange
- Schweißwerkzeuge
- Arbeitsschutzkleidung
Weitere Informationen zum Thema E-Hand-Schweißen finden Sie in unserem Schweißlexikon.