Basi dell'elettrodo rivestito (MMA)
- Indicazioni generali sulla saldatura con elettrodo rivestito
- Tipo di corrente
- Tipo di elettrodo
- Proprietà dei tipi di rivestimento
- La corretta saldatura con elettrodo rivestito
- Accensione dell’arco
- Posizionamento dell’elettrodo
- Soffio d'arco magnetico
- Parametri di saldatura
- Valori della corrente in funzione del diametro dell’elettrodo
- Attrezzatura necessaria
Informazioni generali
La saldatura manuale con elettrodo (processo numero 111) è un processo di saldatura per fusione e, più precisamente, un processo di saldatura ad arco con elettrodo di metallo. La normativa ISO 857-1 (edizione 1998) spiega il processo di saldatura di questo gruppo basandosi sulla traduzione inglese:
Saldatura ad arco con elettrodo di metallo: il processo di saldatura ad arco utilizza un elettrodo consumabile. Saldatura ad arco con elettrodo di metallo senza protezione del gas: processo di saldatura ad arco con elettrodo di metallo senza gas di protezione aggiunto dall’esterno e saldatura manuale ad arco con elettrodo di metallo: Saldatura ad arco con elettrodo di metallo eseguita manualmente con l’utilizzo di un elettrodo rivestito.
In Europa l’ultimo processo menzionato è noto come saldatura manuale ad arco o saldatura manuale con elettrodo rivestito (in gergo comune anche saldatura con elettrodo). In lingua inglese il processo è noto con le abbreviazioni MMA o MMAW (Manual Metal Arc Welding). Questo procedimento è caratterizzato dalla formazione dell’arco tra un elettrodo consumabile e il bagno di fusione. Non presenta alcuna protezione esterna, infatti qualsiasi protezione dall’atmosfera proviene dall’elettrodo. L’elettrodo funge, dunque, da supporto per l’arco e da metallo di apporto. Il rivestimento forma scorie e/o gas di protezione che, tra le altre cose, proteggono la goccia che viene trasferita e il bagno di fusione dalla penetrazione di gas atmosferici come ossigeno, azoto e idrogeno.
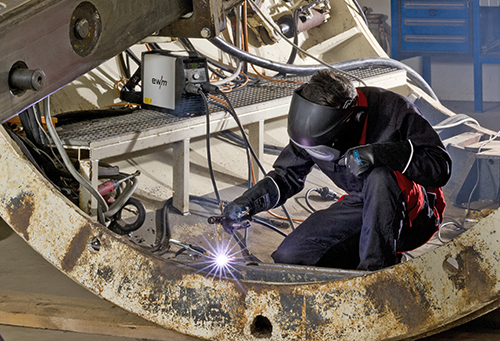
Tipo di corrente
Per la saldatura ad arco (saldatura manuale con elettrodo) è possibile utilizzare sia corrente continua sia corrente alternata, tuttavia, non tutti i tipi di rivestimento degli elettrodi cilindrici possono essere saldati con corrente alternata di forma sinusoidale, ad esempio gli elettrodi non puramente basici. Durante la saldatura in corrente continua, con la maggior parte dei tipi di elettrodo il polo negativo viene collegato all’elettrodo, mentre il polo positivo viene collegato al pezzo da lavorare. Anche in questo caso l’unica eccezione è rappresentata dagli elettrodi basici. Infatti, questo tipo di elettrodi vengono saldati in modo migliore sul polo positivo. Lo stesso vale per certi produttori di elettrodi di cellulosa. Maggiori informazioni al riguardo sono riportate nella sezione Tipi di elettrodi. L’elettrodo è l’attrezzo del saldatore. Egli sposta l’arco che si forma sull’elettrodo nel giunto di saldatura e fonde i bordi di giunzione (Figura 2). In base al tipo di giunto e allo spessore del materiale base è necessario utilizzare diversi valori della corrente. Gli elettrodi rivestiti sono disponibili con diversi diametri e lunghezze, poiché la capacità di carico della corrente degli elettrodi è determinata dal relativo diametro e della relativa lunghezza. La tabella 1 mostra le dimensioni conformi alla norma DIN EN 759. È possibile utilizzare correnti di saldatura più elevate con diametri maggiori dell’anima dell’elettrodo.
Tipi di elettrodo
Esistono elettrodi cilindrici con rivestimenti di composizioni molto diverse. La struttura del rivestimento determina le caratteristiche di fusione dell'elettrodo, le sue caratteristiche di saldatura e la qualità del materiale di saldatura (informazioni dettagliare alla sezione "Quali elettrodi per quale scopo" . In conformità alla norma DIN EN 499 li per gli elettrodi rivestiti adatti alla saldatura di acciai non legati sono disponibili diversi tipi di rivestimento. A tale proposito occorre distinguere tra tipi base e tipi misti. Le lettere utilizzate per la denominazione traggono origine dai termini inglesi. Le lettere hanno il seguente significato: C=cellulose (cellulosico), A=acid (acido), R=rutile (rutilico) e B=basic (basico). In Europa il rivestimento rutilico ricopre un ruolo dominante. Gli elettrodi cilindrici possono avere un rivestimento sottile, medio o spesso. Con gli elettrodi rutilici, che sono disponibili con rivestimenti di tutti e tre gli spessori, gli elettrodi con rivestimento spesso sono identificati dalle lettere RR per consentire una migliore distinzione. Purtroppo, gli elettrodi cilindrici legati e fortemente legati spesso non dispongono di una tale varietà di rivestimenti. Con gli elettrodi cilindrici impiegati per la saldatura di acciai inossidabili, che sono definiti nella norma DIN EN 1600, è possibile fare una distinzione, ad esempio, solo tra gli elettrodi rutilici e basici. Lo stesso avviene con gli elettrodi cilindrici utilizzati per la saldatura di acciai resistenti alle alte temperature (DIN EN 1599), tuttavia in questo caso tra gli elettrodi rutilici vi sono tipi di rivestimento composti da materiali misti rutilbasici, benché non sia specificamente indicato. Ad esempio, questo è il caso di elettrodi che possiedono migliori caratteristiche di saldatura in condizioni particolarmente difficili. Gli elettrodi cilindrici impiegati per la saldatura di acciai altamente resistenti (DIN EN 757) sono disponibili solamente con un rivestimento basico.
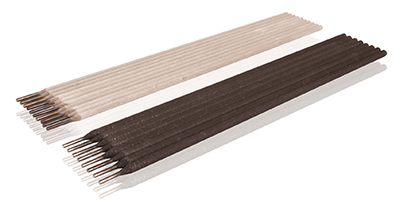
Proprietà dei tipi di rivestimento
La composizione e lo spessore del rivestimento influiscono in particolare modo sulle caratteristiche di saldatura. Ciò riguarda sia la stabilità dell’arco sia il trasferimento del materiale durante la saldatura e la viscosità della scoria e del bagno di fusione. Risulta di particolare importanza la dimensione della goccia che passa nell'arco.
L'immagine mostra in modo schematico la transizione a goccia dei quattro principali tipi di rivestimenti: Cellulosa (a), rutile (b), acido (c), basico (d).
Il rivestimento è costituito in prevalenza da elementi organici, che bruciano nell’arco formando il gas di protezione per proteggere il punto di saldatura. Dato che il rivestimento è composto da una quantità ridotta di materiali che stabilizzano l’elettrodo ad eccezione della cellulosa e di altri materiali organici, non vengono prodotte molte scorie. I tipi cellulosici sono particolarmente adatti per le saldature con cordone verticale discendente, poiché non è necessario preoccuparsi dello scorrimento delle scorie.
Il tipo acido (A), il cui rivestimento è costituito in prevalenza da minerali ferrosi e manganesiferi, offre all’atmosfera dell’arco maggiori quantità di ossigeno. L’ossigeno viene assorbito anche dal materiale di saldatura garantendo la diminuzione della tensione superficiale. Si ottiene, quindi, un trasferimento del materiale estremamente fine, a spruzzi e un materiale di saldatura fluido. Gli elettrodi di questo tipo non sono quindi adatti per la saldatura in condizioni particolarmente difficili. L’arco è anche estremamente “caldo”, consente di raggiungere elevate velocità di saldatura, ma tende a formare solchi dovuti alla penetrazione. Per quanto riguarda la Germania, gli svantaggi descritti hanno condotto alla riduzione dell’utilizzo di elettrodi cilindrici di tipo acido puro.
Al loro posto è stato introdotto il tipo rutilacido (RA), un tipo misto tra elettrodi acidi e rutilici. L’elettrodo ha, infatti, le corrispondenti caratteristiche di saldatura. Il rivestimento del tipo rutilico (R/RR) è costituito in prevalenza da biossido di titanio sotto forma di minerali, quali rutilio (TiO2) o ilmenite (TiO2 . FeO), o anche da biossido di titanio artificiale. Gli elettrodi di questo tipo sono caratterizzati da un trasferimento del materiale con gocce di piccole e medie dimensioni, una fusione stabile e senza spruzzi, una formazione del cordone molto fine, una buona eliminazione delle scorie e da una buona riaccensione. L’ultima caratteristica è rispettata solo con gli elettrodi rutilici con un alta percentuale di TiO2 nel rivestimento. Ciò significa che con un elettrodo già fuso è possibile effettuare una riaccensione senza allontanare il cratere di rivestimento. La pellicola di scorie che si è formata nel cratere possiede, con un contenuto di TiO2 sufficientemente elevato, una conduttività elettrica pari a un semiconduttore, in modo che posizionando il bordo del cratere sul pezzo da lavorare passi un quantitativo di corrente tale che l’arco possa accendersi senza che l’anima venga a contatto con il pezzo da lavorare. Una riaccensione spontanea ricopre una notevole importanza quando il processo di saldatura viene interrotto frequentemente, ad esempio con cordoni corti,.
In questo gruppo di elettrodi, oltre al tipo rutilico puro, sono presenti alcuni tipi composti da materiali misti. Di particolare interesse è il tipo rutilcellulosico (RC) in cui una parte del rutilio è stata sostituita dalla cellulosa. Dato che durante la saldatura la cellulosa brucia, la formazione di scorie è notevolmente ridotta. Dunque, questo tipo può essere utilizzato anche per la saldatura in cordone verticale discendente (pos. PG). Possiede però buone caratteristiche di saldatura anche in molte altre posizioni.
Un altro tipo composto da materiali misti è quello rutilbasico (RB). Questo tipo è caratterizzato da un rivestimento più sottile rispetto al tipo RR. Questa caratteristica e la particolare caratteristica delle scorie rendono il tipo rutilbasico particolarmente adatto per la saldatura in posizione verticale ascendente (PF). L’ultimo tipo è quello basico (B). In questo caso il rivestimento è costituito in gran parte dagli ossidi basici del calcio (CaO) e del magnesio (MgO), a cui viene aggiunta fluorite spatica (CaF2) come riduttore di scorie. L’elevato contenuto di fluorite spatica compromette la qualità della saldatura in corrente alternata. Gli elettrodi basici puri non possono perciò essere saldati in corrente alternata di forma sinusoidale, tuttavia esistono anche tipi composti da materiali misti con un contenuto ridotto di fluorite spatica nel rivestimento, che possono essere utilizzati con questo tipo di corrente. Il trasferimento del materiale degli elettrodi basici utilizza gocce di medie e grosse dimensioni e il bagno di fusione è viscoso. L’elettrodo può essere saldato in tutte le posizioni. Tuttavia, i cordoni prodotti risultano leggermente rinforzati e ondulati in modo più marcato a causa della maggiore viscosità del materiale di saldatura. Il materiale di saldatura possiede buone caratteristiche di solidità.
I rivestimenti basici sono igroscopici. È necessario assicurarsi che gli elettrodi vengano immagazzinati in luoghi asciutti. Gli elettrodi che assorbono l’umidità devono essere messi a seccare. Tuttavia, se gli elettrodi vengono saldati quando sono asciutti, il materiale di saldatura ha un contenuto di idrogeno molto basso. Oltre agli elettrodi cilindrici con un rendimento normale (<105%) sono disponibili elettrodi che, grazie alla polvere ferrosa aggiunta sul rivestimento, sono caratterizzati da un rendimento più alto, in generale >160%. Questo tipo di elettrodi è conosciuto come tipo in polvere ferrosa o anche come elettrodi ad alto rendimento. Grazie all’elevata velocità di fusione questi elettrodi sono adatti per numerosi impieghi in quanto economicamente più convenienti rispetto agli elettrodi normali; tuttavia, generalmente il loro utilizzo è limitato alla posizione verticale (PA) e orizzontale (PB).
La corretta saldatura con elettrodo rivestito
Il saldatore necessita di una buona formazione, non solo dal punto di vista della pratica, ma anche da quello delle competenze teoriche, al fine di evitare di commettere errori. A questo scopo sono rilevanti le direttive per la formazione proposte dal “International Institute of Welding (IIW)”, l’Associazione internazionale per la saldatura, e dalle associazioni nazionali. Prima di iniziare la saldatura i pezzi da lavorare vengono generalmente saldati con un processo di puntatura. I punti di saldatura devono essere sufficientemente lunghi e spessi, in modo che i pezzi da lavorare non possano contrarsi eccessivamente durante la saldatura e i punti di saldatura non possano rompersi.
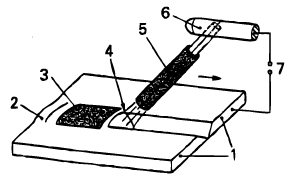
- Pezzo da lavorare
- Cordone di saldatura
- Scoria
- Arco
- Elettrodo rivestito
- Portaelettrodo
- Fonte della corrente di saldatura
Accensione dell’arco
Nella saldatura con elettrodo rivestito il processo di saldatura viene attivato mediante l’accensione a contatto. Per chiudere il circuito elettrico, è necessario generare innanzitutto un cortocircuito tra l’elettrodo ed il pezzo da lavorare e immediatamente dopo l’elettrodo deve essere leggermente sollevato; in seguito l’arco si accende. Il processo di accensione non deve mai avvenire all’esterno del giunto, ma generalmente in quei punti che vengono immediatamente fusi dopo la formazione dell’arco. Infatti, nei punti di accensione, in cui ciò non accade, possono formarsi delle cricche nei materiali particolarmente sensibili a causa dell’improvviso riscaldamento. Con gli elettrodi basici, che hanno la tendenza alla porosità iniziale, l’accensione deve avvenire sensibilmente prima dell’inizio della saldatura. Successivamente l’arco viene riportato al punto di inizio del cordone e durante la saldatura le prime gocce depositate, che sono in prevalenza porose, vengono nuovamente fuse.
Posizionamento dell’elettrodo
L’elettrodo viene posizionato perpendicolare o leggermente inclinato rispetto alla superficie della lamiera. Viene quindi inclinato leggermente nella direzione di saldatura. La lunghezza visibile dell’arco, ovvero la distanza tra il bordo del cratere e la superficie del pezzo da lavorare deve corrispondere praticamente al diametro dell’anima dell’elettrodo. Gli elettrodi basici devono essere saldati con un arco estremamente corto (distanza = 0,5 x diametro dell’anima). Per garantire questa condizione, questi elettrodi devono essere posizionati con un’inclinazione maggiore rispetto agli elettrodi rutilici. Nella maggior parte delle posizioni, vengono saldati cordoni sottili o viene utilizzato un movimento leggermente oscillante con un’ampiezza maggiore del giunto. Solamente nella posizione PF vengono eseguiti cordoni oscillanti lungo l’intera ampiezza del giunto. Solitamente l’elettrodo viene posizionato a rovescio, mentre nella posizione PF viene posizionato diritto.
- Giunto di saldatura
- Elettrodo rivestito
- Materiale di saldatura liquido
- Scoria liquida
- Scoria solidificata
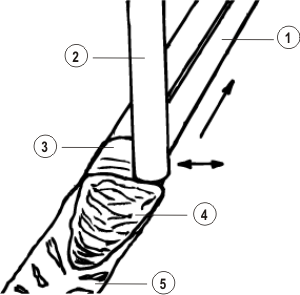
Soffio d'arco magnetico
Il soffio d'arco si verifica nel momento in cui l'arco deviando dal suo asse mediano si allunga ed emette un sibilo. Questa deviazione da luogo a delle irregolarità. È possibile che la penetrazione non sia adeguata e nei processi di saldatura che producono scorie, possono verificarsi inclusioni di scorie nel cordone a causa dello scorrimento delle scorie. La deviazione avviene tramite forze che si generano dal campo magnetico circostante. Come ogni conduttore della corrente, anche l’elettrodo e l’arco sono circondati da un campo magnetico toroidale – questo viene deviato nell’area dell’arco al momento del contatto con il materiale base. In questo modo le linee di forza magnetiche sul lato interno vengono compresse, mentre sul lato esterno vengono ampliate. L'arco si sposta nell'area della densità della linea di flusso ridotta. In seguito si allunga ed emette un sibilo a causa della maggiore tensione dell'arco. Il polo opposto genera dunque un effetto repulsivo sull'arco. Si genera dunque un'altra forza magnetica, dovuta al fatto che l'ampliamento del campo magnetico diventa più facile in un materiale ferromagnetico che nell'aria. Perciò l'arco viene attratto da grandi masse ferrose. Ciò si evidenzia, ad es., quando durante la saldatura su un materiale magnetizzabile, l'arco viene deviato all'interno in corrispondenza delle estremità della lamiera. La deviazione dell'arco può essere contrastata inclinando l'elettrodo. Poiché il soffio d'arco durante la saldatura con corrente continua è particolarmente grande, è possibile, mediante la saldatura in corrente alternata, evitare che ciò si verifichi o almeno ridurre notevolmente il soffio. Durante la saldatura dei punti di giunzione il soffio d'arco può essere particolarmente forte a causa delle masse ferrose circostanti. In questo caso ciò si rivela utile se il flusso magnetico è supportato da punti di saldatura ravvicinati, ma non troppo corti.
Parametri di saldatura
Nella saldatura manuale con elettrodo viene impostato solo il valore della corrente, mentre la tensione dell’arco si ottiene dalla lunghezza dell’arco adottata dal saldatore. Durante l’impostazione del valore della corrente, è necessario tenere presente la capacità di carico di corrente del diametro dell’elettrodo utilizzato. In questo frangente è valida la regola, secondo cui i valori limite inferiori vengono utilizzati per la saldatura delle passate alla radice e per la posizione PF, mentre i valori limite superiori vengono utilizzati per le restanti posizioni e le passate di riempimento e finali. Con l’incremento dei valori della corrente, aumenta la velocità di fusione e, di conseguenza, anche la velocità di saldatura. Anche la penetrazione aumenta all’aumentare della corrente. I valori della corrente riportati nella tabella sono validi unicamente per gli acciai non legati e debolmente legati. Con gli acciai fortemente legati e i materiali a base di nickel, è necessario impostare dei valori più bassi a causa dell’elevata resistenza elettrica dell’anima dell’elettrodo.
Valori della corrente in funzione del diametro dell’elettrodo
Occorre rispettare le seguenti regole per il calcolo dei singoli valori della corrente:
20-40 x Ø
- Con un diametro di 2,0 mm il valore della corrente dovrebbe essere 40-80 A
- Con un diametro di 2,5 mm il valore della corrente dovrebbe essere 50-100 A
30-50 x Ø
- Con un diametro di 3,2 mm il valore della corrente dovrebbe essere 90-150 A
- Con un diametro di 4,0 mm il valore della corrente dovrebbe essere 120-200 A
- Con un diametro di 5,0 mm il valore della corrente dovrebbe essere 180-270 A
35-60 x Ø
- Con un diametro di 6,0 mm il valore della corrente dovrebbe essere 220-360 A
Per il successo della saldatura con elettrodo rivestito è necessaria la seguente attrezzatura:
- Fonte della corrente di saldatura
- Portaelettrodo
- Elettrodo rivestito
- Morsetto per pezzo da lavorare/pinza di massa
- Attrezzi di saldatura
- Abbigliamento protettivo da lavoro
Ulteriori informazioni sulla saldatura con elettrodo rivestito sono riportate nel nostro Glossario della saldatura.