Elektrode lassen (MMA) basisprincipes
- Algemene informatie over elektrode lassen
- Stroomtype
- Elektrodetype
- Eigenschappen van bekledingstypes
- Correct elektrode lassen
- De vlamboog ontsteken
- De elektrode voeren
- Magnetische blaaswerking
- Lasparameters
- Stroomsterkte naargelang de elektrodediameter
- Vereiste uitrusting
Algemeen
Het elektrode lassen (procesnummer 111) behoort tot het smeltlasproces en is ook ingedeeld in het metaal-vlambooglasproces. NEN-ISO 857-1 (editie 1998) verklaart de uit het Engels vertaalde lasprocessen van deze groep als volgt:
Metaal-vlambooglassen: Vlambooglasproces onder toepassing van een verbruikende elektrode. Metaal-vlambooglassen zonder gasbescherming: Metaal-vlambooglasproces zonder externe toevoer van beschermgas en handmatig metaal-vlambooglassen: Met de hand gevoerd metaal-vlambooglassen onder toepassing van een beklede elektrode.
In Duitsland wordt het laatstgenoemde proces aangeduid als vlambooghandlassen of handmatig elektrode lassen (in de omgangstaal elektrode lassen genoemd). In het Engelse taalgebied staat het proces bekend als MMA of MMAW (Manual Metal Arc Welding). Kenmerkend voor dit proces is dat de vlamboog tussen een afsmeltende elektrode en het lasbad brandt. Er is geen externe bescherming. De enige beschermende werking tegen de atmosfeer wordt door de elektrode gevormd. De elektrode is daarbij de vlamboogdrager en het lastoevoegmateriaal. De bekleding vormt slakken die en/of beschermgassen die in het lasbad druppelen en het lasbad beschermen tegen het binnendringen van de atmosferische gassen zuurstof, stikstof en waterstof.
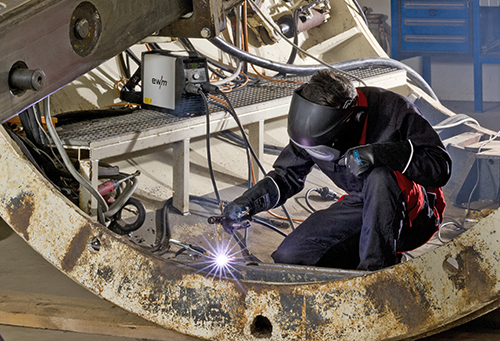
Stroomtype
Voor vlambooghandlassen (elektrode lassen) kan in principe zowel gelijkstroom als wisselstroom worden gebruikt, maar niet alle bekledingstypes van staafelektroden kunnen met sinusvormige wisselstroom worden gelast, zoals zuiver basische elektroden. Bij het lassen met gelijkstroom wordt bij de meeste elektrodetypes de minpool aan de elektrode en de pluspool op het werkstuk aangesloten. Een uitzondering daarop zijn de basische elektroden. Die kunnen aan de pluspool worden gelast. Hetzelfde geldt voor bepaalde fabricaten uit cellulose-elektroden. Voor meer informatie hierover leest u het hoofdstuk Elektrodetypes. De elektrode is het gereedschap van de lasser. Hij voert de elektrode naar de brandende vlamboog in de lasvoeg en smelt daarbij de voegranden, zie afbeelding 2. Naargelang het voegtype en de basismateriaaldikte worden verschillende stroomsterktes vereist. Aangezien de stroombelastbaarheid van de elektrode afhankelijk is van de diameter en lengte van de elektrode, zijn de staafelektroden in verschillende diameters en lengtes te verkrijgen. Tabel 1 geeft de in NEN-EN 759 gestandaardiseerde afmetingen weer. Hoe groter de diameter van de kernstaaf, hoe hoger de toe te passen lasstroom.
Elektrodetypes
Er bestaan staafelektroden met bekledingen in zeer verschillende samenstellingen. De opbouw van de bekleding bepaalt het afsmeltkarakter van de elektrode, de laseigenschappen en de kwaliteitswaarden van het lasmateriaal (gedetailleerde informatie in het hoofdstuk "Welke elektrode voor welke toepassing" . Volgens de norm NEN-EN 499 zijn er verschillende bekledingstypes voor staafelektroden om ongelegeerde staalsoorten te lassen. Daarbij wordt er onderscheid gemaakt tussen basistypes en mengtypes. De gebruikte letters voor de benaming vinden hun oorsprong in Engelse begrippen. Hier betekent C=cellulose (cellulose), A=acid (zuur), R=rutile (rutiel) en B=basic (basisch). In Duitsland wordt voornamelijk het rutieltype gebruikt. Staafelektroden kunnen een dunne, middelmatig dikke en dikke bekleding hebben. Bij rutiele elektroden, die in alle drie bekledingsdiktes beschikbaar zijn, worden de elektrode met dikke bekleding voor een duidelijker onderscheid met RR aangeduid. Bij gelegeerde en hooggelegeerde staafelektroden bestaat deze veelvoud van bekledingstypes niet. Bij staafelektroden voor het lassen van corrosievaste staalsoorten, die zijn gestandaardiseerd in de norm NEN-EN 1600, en bij staafelektroden voor het lassen van hittevaste staalsoorten (NEN-EN 1599) wordt alleen een onderscheid gemaakt tussen rutiele en basische elektroden. Rutielelektroden van het rutiel-basische mengtype worden niet specifiek behandeld. Deze elektroden worden bijv. gebruikt voor betere laseigenschappen in geforceerde posities. Staafelektroden voor het lassen van staalsoorten (NEN-EN 757) met hoge sterkte zijn uitsluitend verkrijgbaar met basische bekleding.
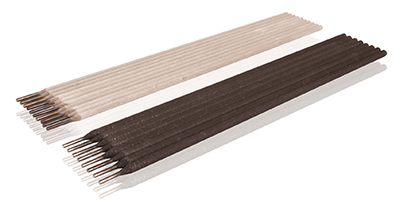
Eigenschappen van bekledingstypes
De samenstelling en de dikte van de bekleding zijn in bijzondere mate van invloed op de laseigenschappen. Dit is zowel van toepassing op de stabiliteit van de vlamboog als op de materialovergang bij het lassen en de viscositeit van slakken en het lasbad. Vooral de grootte van in de vlamboog overlopende druppels is daarbij zeer belangrijk.
De afbeelding geeft schematisch de druppelovergang van vier basistypes van bekledingen weer: cellulose (a), rutiel (b), zuur (c), basisch (d).
De bekleding bestaat overwegend uit organische bestanddelen, die in de vlamboog verbranden en daarbij het beschermgas ter bescherming van de lasplek vormen. Aangezien de bekleding, behalve cellulose en andere organische stoffen, slechts kleine hoeveelheden vlamboogstabiliserende stoffen bevat, ontstaan er nauwelijks slakken. Cellulosetypes zijn vooral geschikt voor verticaal neergaand lassen, omdat er geen sprake is van slakkenvoorloop.
Het zure type (A), waarvan de bekleding grotendeels uit ijzer- en mangaanertsen bestaat, biedt grote hoeveelheden zuurstof aan vlamboogatmosferen. Het zuurstof wordt ook door het lasmateriaal opgenomen en vermindert daardoor de oppervlaktespanning. Het resultaat is een zeer fijne, motregenachtige materialovergang en dunvloeibaar lasmateriaal. Elektroden van dit type zijn daarom niet geschikt voor het lassen in geforceerde posities. De vlamboog wordt ook heet en biedt weliswaar hoge lassnelheden, maar heeft de neiging om randinkartelingen te vormen. De beschreven nadelen hebben ertoe geleid dat staafelektroden van het zure type nog nauwelijks in Duitsland worden gebruikt.
In plaats daarvan wordt het rutielzure type (RA) gebruikt, een mengtype tussen de zure en rutiele elektrode. De elektrode heeft ook de dienovereenkomstige laseigenschappen De bekleding van het rutieltype (R/RR) bestaat voor een groot deel uit titaanoxide in de vorm van de mineralen rutiel (TiO2) of ilmeniet (TiO2 . FeO) of ook van kunstmatige titaandioxide. De elektroden van dit type kenmerken zich door een fijne tot middelgrote materiaalovergang, een rustig spatarm afsmelten, een zeer fijne lasnaadtekening, een goede verwijderbaarheid van slakken en een goed herontstekingsgedrag. De laatstgenoemde is in deze vorm uitsluitend waar te nemen bij rutiele elektroden met hoog TiO2-gehalte in de bekleding. Dit betekent dat bij een reeds aangesmolten elektrode een herontsteking zonder verwijdering van de krater mogelijk is. De in de krater gevormde slakkenfilm heeft bij een hoge TiO2-gehalte bijna hetzelfde geleidingsvermogen als een halfgeleider, zodat bij het oprichten van de kraterrand op het werkstuk zoveel stroom stroomt dat de vlamboog kan ontsteken, zonder dat de kernstaaf het werkstuk aanraakt. Een dergelijke spontane herontsteking is dan altijd belangrijk wanneer het lasproces, bijv. bij korte lasnaden, vaak worden onderbroken.
Naast het zuivere rutieltype heeft deze elektrodegroep nog enkele mengtypes, zoals het rutiel-cellulosetype (RC), waarbij een deel van het rutiel door cellulose wordt vervangen. Aangezien cellulose tijdens het lassen verbrandt, worden er minder slakken gevormd. Dit type kan daarom ook bij verticaal neergaand lassen (pos. PG) worden gebruikt. Maar ook voor de andere posities heeft dit type goede laseigenschappen.
Een ander mengtype is het rutielbasische type (RB). Deze is iets dunner bekleed dan het RR-type. Dit en de bijzondere slakkenkarakteristiek maken dit type uiterst geschikt voor verticaal opgaand lassen (positie PF). Het laatste draadelektrodetype is het basische type (B). Hierbij bestaat de bekleding grotendeels uit basische calciumoxiden (CaO) en magnesiumoxiden (MgO), waaraan als slakkenverdunner vloeispaat (CaF2) wordt toegevoegd. Het vloeispaat belemmert bij hogere gehaltes de lasbaarheid met wisselstroom. Zuiver basische elektroden kunnen daarom niet met sinusvormige wisselstroom worden gelast, maar er zijn ook mengtypes met minder vloeispaat in de bekleding die voor dit stroomtype kunnen worden gebruikt. De materiaalovergang van de basische elektroden is middelgrof- tot grofdruppelig en het lasbad is dikvloeibaar. De elektrode is geschikt voor het lassen in alle posities. De rupsen zijn echter vanwege de grotere viscositeit van het lasmateriaal iets overdekkend en grof geveerd. Het lasmateriaal heeft zeer goede taaiheidseigenschappen.
Basische bekledingen zijn hygroscopisch. De elektroden moeten daarom zorgvuldig en op een droge plek worden opgeslagen. Vochtig geworden elektroden moeten eerst worden gedroogd. Wanneer de elektroden droog worden gelast, bezit het lasmateriaal een zeer laag waterstofgehalte. Naast staafelektroden met normale opbrengst (<105 %) zijn er ook elektroden met ijzerpoeder die via de bekleding worden toegevoerd en een hogere opbrengst hebben, meestal >160 %. Dergelijke elektroden worden ook elektroden van het ijzerpoedertype of high performance-type genoemd. Door hun groter afsmeltvermogen zijn ze voor vele toepassingen voordeliger dan normale elektroden, maar hun toepassing is over het algemeen tot de onder de hand- (PA) en uit de zij-posities (PB) beperkt.
Correct elektrode lassen
De lasser moet goed zijn opgeleid, en niet alleen in praktisch opzicht, maar hij moet ook over de desbetreffende vakkundige kennis beschikken om fouten te voorkomen. De opleidingsrichtlijnen van de DVS – Deutscher Verband für Schweißen und verwandte Verfahren e.V. worden wereldwijd erkend en werden ook door de internationale lasvereniging (IIW) overgenomen. Doorgaans worden de werkstukken voorafgaand aan het lassen vastgezet. De hechtpunten moeten een bepaalde lengte en dikte hebben, zodat de werkstukken bij het lassen niet buitensporig kunnen samentrekken en dat hechtpunten niet kunnen scheuren.
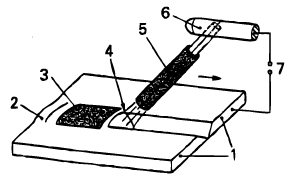
- Werkstuk
- Lasnaad
- Slakken
- Vlamboog
- Beklede elektrode
- Elektrodehouder
- Lasstroombron
De vlamboog ontsteken
Het lasproces wordt bij elektrode lassen door een contactontsteking ingeleid. Om de stroomkring te sluiten, moet er eerst een kortsluiting worden gemaakt tussen de elektrode en het werkstuk, en daarna moet de elektrode lichtjes worden opgetild – de vlamboog wordt ontstoken. De ontsteking mag nooit buiten de voeg plaatsvinden, maar over het algemeen op plekken die na het branden van de vlamboog onmiddellijk worden afgesmolten. Bij de ontsteking van de vlamboog op andere plekken kunnen er vooral bij gevoelige materialen scheuren ontstaan als gevolg van de plotselinge opwarming. Bij basische elektroden met poreuze eigenschappen, moet de ontsteking zelfs vóór het werkelijke begin van het lassen worden uitgevoerd. Daarna wordt de vlamboog teruggevoerd naar het aanvangspunt van de lasnaad en bij het verdere lasproces worden de eerste afgezette druppels die het meest poreus zijn, opnieuw gesmolten.
De elektrode voeren
De elektrode wordt loodrecht of licht schuin op het plaatoppervlak aangezet. De elektrode wordt licht in de lasrichting gekanteld. De zichtbare vlambooglengte, d.w.z. de afstand tussen de kraterrand en het werkstukoppervlak moet daarbij ongeveer overeenkomen met de diameter van de kernstaaf. Basische elektroden moeten met een zeer korte vlamboog worden gelast (afstand = 0,5 x kernstaafdiameter). Om dit te garanderen, moeten ze steiler worden gevoerd dan rutiele elektroden. In de meeste posities worden streeplasrupsen gelast of wordt er licht gependeld over een opgaand groter wordende voegbreedte. Alleen in de PF-positie worden pendellasrupsen over de volledige breedte van de voeg getrokken. Over het algemeen wordt er slepend gelast. Alleen in de PF-positie wordt de elektrode stekend aangelegd.
- Lasvoeg
- Staafelektrode
- Vloeibaar lasmateriaal
- Vloeibare slak
- Verharde slak
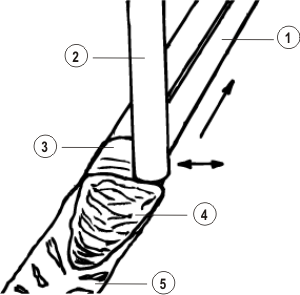
Magnetische blaaswerking
Onder blaaswerking wordt een fenomeen begrepen, waarbij de vlamboog door afbuiging uit de middenas wordt verlengd en u een sissend geluid hoort. Door deze afbuiging kunnen oneffenheden ontstaan. Zo kan de inbranding inadequaat worden en bij slakvoerende lasprocessen kunnen door slakvoorloop in de lasnaad slakinsluitsels ontstaan. Afbuigingen zijn het gevolg van krachten uit het omringende magnetische veld. Zoals bij andere stroomgeleidende geleiders worden ook de elektrode en de vlamboog door een ringvormig magnetisch veld omgeven – dit wordt in het bereik van de vlamboog omgeleid naar het basismateriaal. Hierdoor worden de magnetische krachtlijnen aan de binnenkant gecomprimeerd en aan de buitenkant verbreed. De vlamboog wijkt af in gebieden met een verminderde lijndichtheid. Daarbij wordt de vlamboog langer en er wordt door de verhoogde vlamboogspanning een sissend geluid gegenereerd. De tegenpool oefent dus een afstotend effect uit op de vlamboog. Een andere magnetische kracht zorgt dat het magnetische veld in ferromagnetisch materiaal beter wordt verspreid dan in de lucht. De vlamboog wordt daarom door de grote ijzermassa aangetrokken. Dit is bijv. zichtbaar bij het lassen van magnetiseerbaar materiaal waar de plaatuiteinden naar binnen afbuigen. De afbuiging van de vlamboog kan worden tegengaan door de elektrode onder de juiste hoek te plaatsen. Aangezien de blaaswerking bij het lassen met gelijkstroom bijzonder groot is, is het mogelijk om afbuiging te voorkomen of op zijn minst aanzienlijk te verminderen door te lassen met wisselstroom. Vanwege de omringende ijzermassa bij het lassen van grondlagen kan de blaaswerking zeer sterk worden. Hier helpt het om de magnetische flux te ondersteunen door dichtbij elkaar liggende, niet te korte hechtpunten te gebruiken.
Lasparameters
Bij elektrode lassen wordt alleen de stroomsterkte ingesteld. De vlamboogspanning is het resultaat van de vlambooglengte die door de lasser worden aangehouden. Bij de instelling van de stroomsterkte moet er rekening worden gehouden met de gebruikte elektrodediameter. De regel is dat de onderste grenswaarden van toepassing zijn op het lassen van grondlagen en de PF-positie, terwijl de bovenste limiet van toepassing is op de overige posities en de vul- en deklagen. Naarmate de stroom toeneemt, wordt het afsmeltvermogen en de daarmee verbonden lassnelheid verhoogd. Bij een stijgende stroom neemt ook de inbranding toe. De aangegeven stroomsterktes gelden alleen voor ongelegeerde en laaggelegeerde staalsoorten. Bij hooggelegeerde staalsoorten en nikkelbasismaterialen moeten vanwege de grotere elektrische weerstand van de kernstaaf lagere waarden worden ingesteld.
Stroomsterkte naargelang de elektrodediameter
De volgende vuistregels gelden voor de berekening van de afzonderlijke stroomsterktes in A:
20-40 x Ø
- Bij een diameter van 2,0 mm moet de stroomsterkte tussen 40-80 A liggen
- Bij een diameter van 2,5 mm moet de stroomsterkte tussen 50-100 A liggen
30-50 x Ø
- Bij een diameter van 3,2 mm moet de stroomsterkte tussen 90-150 A liggen
- Bij een diameter van 4,0 mm moet de stroomsterkte tussen 120-200 A liggen
- Bij een diameter van 5,0 mm moet de stroomsterkte tussen 180-270 A liggen
35-60 x Ø
- Bij een diameter van 6,0 mm moet de stroomsterkte tussen 220-360 A liggen
Voor adequaat elektrode lassen heeft u de volgende uitrusting nodig:
- Lasstroombron
- Elektrodehouder
- Staafelektrode
- Werkstukklem/aardeklem
- Lasgereedschap
- Veiligheidskleding
Meer informatie over het thema elektrode lassen vindt u in ons laslexicon.