¿Qué gas de protección debe utilizarse en soldaduras TIG y MIG/MAG?
Gas de protección TIG
Como ya sugiere el nombre del proceso, por regla general, la soldadura TIG utiliza gases inertes. Los gases de protección están estandarizados en UNE-EN 439 y según la norma llevan las denominaciones l1, l2 e l3.
El gas de protección que más se utiliza en la soldadura TIG es el argón (I1). El grado de pureza debe ser como mínimo de 99,95%. En metales con excelente conductividad térmica, como el aluminio o el cobre, también se utiliza helio (I2). Si el helio es el gas de protección, el arco voltaico estará más caliente. Pero sobre todo, el calor entre el núcleo y el borde del arco voltaico se distribuye con mayor homogeneidad. El uso de helio puro en soldaduras TIG es raro y se limita a casos especiales; en cambio, desde hace algunos años, se utilizan cada vez más las mezclas de argón y helio (I3) con 25, 50 o 75% de helio. De este modo, por ejemplo, con estructuras de aluminio más gruesas, se reduce la temperatura de calentamiento previo necesaria para lograr una penetración suficiente. En muchos casos, también se puede aumentar la velocidad de soldadura. En la soldadura TIG de aceros inoxidables de cromo-níquel, también se utilizan mezclas de argón/hidrógeno (R1), aunque para evitar los poros, el contenido de hidrógeno debe ser inferior al 5%.
El caudal de gas de protección dependerá del diámetro de la boquilla de gas y de la corriente de aire circundante. Para el argón, como valor de referencia, se puede partir de un caudal volumétrico de 5-10 l/min. En zonas con corrientes de aire (Fig. 4), se requieren en ocasiones grandes caudales. Debido a la menor densidad del helio, cuando se mezclan argón y helio es preciso establecer caudales más altos.
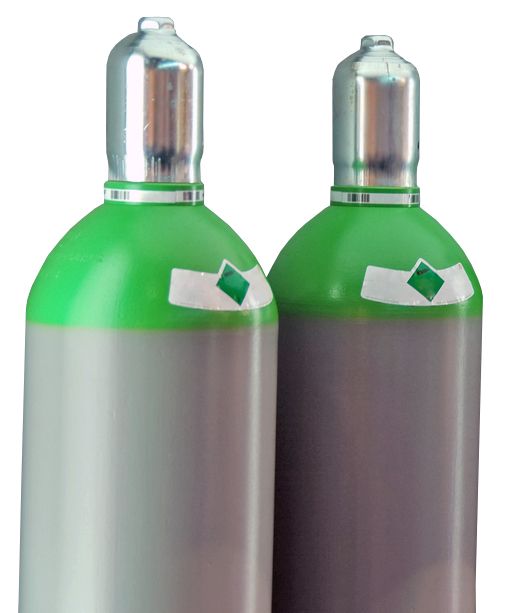
Gas de protección MIG/MAG
Los gases de protección para la soldadura MIG/MAG se encuentran en la norma UNE-EN 439. Esta estandariza todos los gases de protección para soldadura y corte por arco voltaico. Los gases de protección se dividen en siete grupos y en otros subgrupos.
Vista general de los grupos de gases de protección
Grupo R
El grupo R contiene mezclas de argón e hidrógeno con efecto reductor. Además de argón y helio, los gases del Grupo R1 se utilizan para soldaduras TIG y de plasma, mientras que los gases del subgrupo 2, con mayor contenido de hidrógeno (H), se usan para corte de plasma y protección de raíces (mezcla de hidrógeno y nitrógeno).
Grupo I
El Grupo I contiene los gases inertes. Entre ellos, argón (Ar), helio (He) y mezclas de argón y helio. Se emplean para soldaduras TIG, MIG y de plasma y para protección de raíces.
Grupo M
El gran grupo M, que a su vez se subdivide en M1, M2 y M3, aúna gases de mezcla para la soldadura MAG. Cada grupo se divide en 3 o 4 subgrupos. Los gases se clasifican de M1.1 a M3.3 de acuerdo con su comportamiento de oxidación, es decir, M1.1 es el menos oxidante y M3.3 el de mayor oxidación. El componente principal de estos gases es el argón, y en componentes activos, se mezclan el oxígeno (O) o el dióxido de carbono (CO2) o el oxígeno y el dióxido de carbono (gases de tres componentes).
Grupo C
En el rango de gases para soldadura MAG, el Grupo C incluye dióxido de carbono puro y una mezcla de dióxido de carbono y oxígeno. Esto último no es relevante en Alemania. Los gases del Grupo C son los de mayor oxidación, ya que el CO2 se descompone con la alta temperatura del arco voltaico, produciendo monóxido de carbono y grandes cantidades de oxígeno.
Grupo F
Por último, el grupo F incluye nitrógeno (N) y una mezcla de nitrógeno e hidrógeno. Ambos gases se pueden usar para formar y cortar plasma.
Además del comportamiento de oxidación, con la composición del gas también cambian las propiedades eléctricas y físicas en la zona del arco voltaico y, en consecuencia, las propiedades de soldadura. Por ejemplo, si se añade helio al argón, mejorarán la conductividad térmica y la retención térmica de la atmósfera del arco. En ambos casos, el resultado es un arco voltaico de mayor contenido energético y, por ende, un mejor comportamiento de penetración. La mezcla de los componentes activos en los gases de mezcla conduce, entre otros, a una formación de gotas más fina cuando se funde el hilo de soldadura. También mejora la transferencia de calor en el arco voltaico. En este caso, el resultado es también un mejor comportamiento de penetración.
El caudal del gas de protección necesario se puede calcular con una regla general: de 10 a 12 veces el diámetro del hilo en litros/minuto.
En el caso de la soldadura MIG de aluminio, los caudales establecidos son ligeramente superiores a la media debido a la fuerte tendencia del material a oxidarse; para los gases de mezcla Ar/He, los caudales son mucho más altos debido a la baja densidad de helio. La presión del gas de la botella o de la conducción en circuito cerrado se reduce. El caudal establecido se puede leer en un manómetro, calibrado con un difusor, o en un caudalímetro con flotador.
Denominación |
Datos en porcentaje de volumen (% de vol.) |
Uso |
Observaciones |
||||||
Grupo |
Código |
oxidante |
inerte |
reducido |
poco reactivo |
|
|
||
|
|
CO2 |
O2 |
Ar |
He |
H2 |
N2 |
||
R |
1 |
|
|
Resto² |
|
> 0 a 15 |
|
TIG, soldadura de plasma, corte de plasma, protección de raíces |
|
2 |
|
|
Resto² |
|
> 15 a 35 |
|
|||
I |
1 |
|
|
100 |
|
|
|
MIG, TIG, soldadura de plasma, protección de raíces |
inerte |
2 |
|
|
|
100 |
|
|
|||
3 |
|
|
Resto² |
> 0 a 95 |
|
|
|||
M1 |
1 |
> 0 a 5 |
|
Resto² |
|
> 0 a 5 |
|
MAG |
poco oxidante |
2 |
> 0 a 5 |
|
Resto² |
|
|
|
|||
3 |
|
> 0 a 3 |
Resto² |
|
|
|
|||
4 |
> 0 a 25 |
> 0 a 3 |
Resto² |
|
|
|
|||
M2 |
1 |
> 0 a 25 |
|
Resto² |
|
|
|
|
|
2 |
|
> 3 a 10 |
Resto² |
|
|
|
|||
3 |
> 0 a 5 |
> 3 a 11 |
Resto² |
|
|
|
|||
4 |
> 0 a 25 |
> 0 a 8 |
Resto² |
|
|
|
|||
M3 |
1 |
> 25 a 50 |
|
Resto² |
|
|
|
|
|
2 |
|
> 10 a 15 |
Resto² |
|
|
|
|||
3 |
> 5 a 50 |
> 8 a 15 |
Resto² |
|
|
|
|||
C |
1 |
100 |
|
|
|
|
|
muy oxidante |
|
2 |
Resto |
> 0 a 30 |
|
|
|
|
|||
F |
1 |
|
|
|
|
|
100 |
Corte de plasma, protección de raíces |
poco reactivo |
2 |
|
|
|
|
> 0 a 50 |
Resto |
reductor |
Clasificación de gases de protección para corte y soldadura por arco voltaico