Fundamentos de la soldadura TIG
- Datos de interés de la soldadura TIG
- Elección del consumible para soldadura
- Ajuste de la cantidad de gas de protección
- Limpieza de la superficie de la pieza de trabajo
- Encendido del arco voltaico
- Guía de la antorcha TIG
- Posición de soldadura
- Parámetros de soldadura
- Soldadura con impulsos eléctricos
- Equipamiento necesario
Datos de interés de la soldadura TIG
Con respecto a los materiales que se van a procesar, los grosores de pared y las posiciones de soldadura, la soldadura TIG es un proceso de aplicación universal. Permite crear uniones de soldadura de la máxima calidad. El proceso de soldadura TIG: la denominación completa de este proceso es, según la norma DIN 1910, parte 4, soldadura bajo atmósfera inerte de tungsteno. Tiene su origen en Estados Unidos, donde se conoce desde 1936 con el nombre de soldadura por arco de argón. En Alemania no se introdujo hasta después de la Segunda Guerra Mundial. La T de la soldadura TIG corresponde al tungsteno. En comparación con otros procesos de soldadura por fusión, presenta una serie de ventajas interesantes, como su aplicación universal.
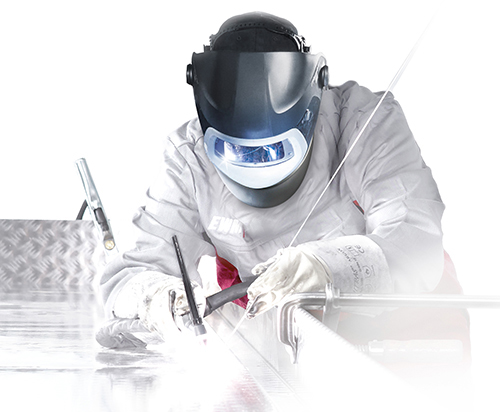
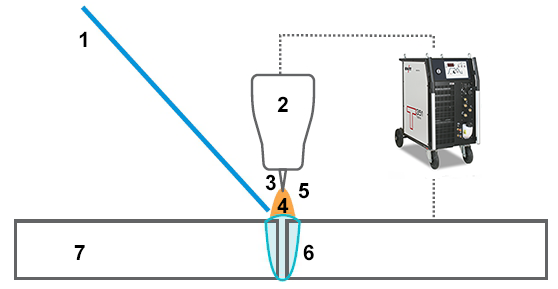
- Varilla de soldadura
- Antorcha
- Electrodo de tungsteno
- Arco voltaico
- Gas de protección
- Baño de soldadura
- Material base
Si un material metálico es adecuado para la soldadura por fusión, podrá unirse con este proceso. Por otro lado, se trata de un proceso muy «limpio» sin apenas proyecciones ni contaminantes; además, si se utiliza correctamente, se garantiza una junta soldada de gran calidad. Otra ventaja especial de la soldadura TIG es que, a diferencia de otros procesos que funcionan con electrodos de fusión, la alimentación de los consumibles de soldadura y la intensidad de corriente no están desaclopados. De este modo, el soldador puede adaptar perfectamente su corriente al trabajo de soldadura y agregar solo tanto consumible de soldadura como necesite en ese momento. Con ello, el proceso está particularmente indicado para soldar pasadas de raíz y en posiciones fijas. Gracias a estas ventajas, el proceso TIG se utiliza hoy con éxito en numerosos sectores del comercio y la industria. Sin embargo, aún se requiere la mano experta de un soldador y un buen entrenamiento para el uso manual. Esta guía pretende explicar las particularidades del proceso y quizás, también, despertar el interés de compañías que aún no lo usan pese a contar con los correspondientes trabajos de soldadura.
Elección del consumible para soldadura
El consumible para soldadura utilizado en soldaduras TIG tiene generalmente forma de varilla y, en métodos completamente mecánicos, se introduce en forma de hilo por un mecanismo de alimentación separado. Por regla general, los consumibles de soldadura se eligen de la misma manera que el material base. Sin embargo, por razones metalúrgicas, con ciertos elementos de aleación es preciso que el consumible sea algo distinto del material base. Por ejemplo, con contenido de carbono, para evitar agrietamientos, este debe mantenerse muy bajo. En estos casos, se habla de consumibles para soldadura del mismo tipo. No obstante, también hay casos en los que se necesitan consumibles de distinta naturaleza. Por ejemplo, cuando se unen aceros C, difíciles de soldar; en ese caso, se usan consumibles austeníticos o incluso aleaciones con base de níquel. El diámetro del consumible de soldadura debe sincronizarse con el trabajo de soldadura. Dependerá del grosor del material y, por lo tanto, también del diámetro del electrodo de tungsteno. Las varillas de soldadura suelen tener 1000 mm de longitud. Se entregan en manojos y para evitar confusiones deben etiquetarse individualmente con DIN o con el nombre comercial.
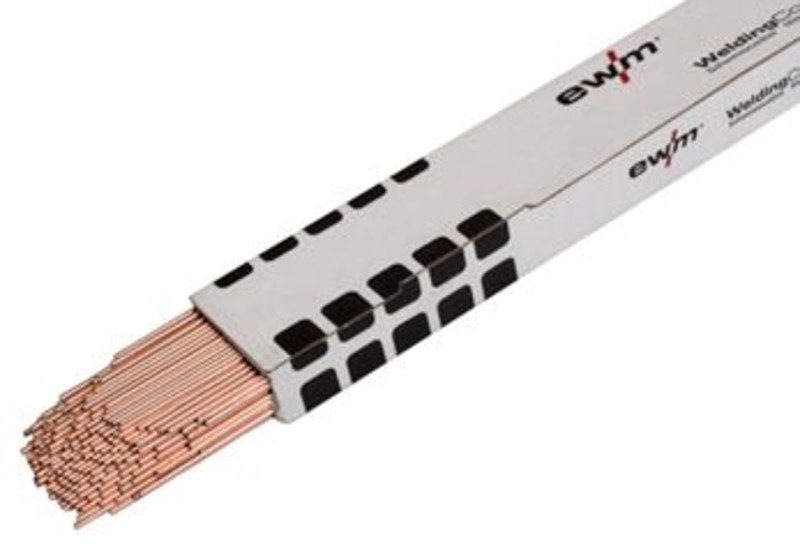
Ajuste de la cantidad de gas de protección
La cantidad de gas de protección se ajusta como caudal volumétrico en I/min. La cantidad de gas de protección dependerá del volumen del baño de soldadura y, por lo tanto, del diámetro del electrodo, del diámetro de la boquilla de gas, de la distancia entre la boquilla y la superficie del material base, de la corriente de aire circundante y del tipo de gas de protección (ver también el apartado dedicado a los gases de protección). Una regla general indica que si se utiliza argón como gas de protección y con los diámetros de electrodos de tungsteno más habituales de 1-4 mm, se deben agregar entre 5 y 10 litros de gas de protección por minuto. El caudal se puede medir indirectamente con manómetros que determinan la presión proporcional al caudal en el difusor. La escala del manómetro se calibra directamente en l/min. Más precisos son los instrumentos que con tubos de vidrio y flotadores miden directamente en el caudal del gas de protección que fluye a la antorcha.
Limpieza de la superficie de la pieza de trabajo
Para obtener un buen resultado de soldadura, antes de empezar a soldar es importante limpiar a fondo los flancos de unión y la superficie de la pieza de trabajo en el ámbito de soldadura. Las superficies deben ser metálicas, sin revestimiento ni grasa, suciedad, óxido o pintura. Siempre que sea posible, se eliminarán también las capas de cascarilla. En muchos casos, basta con un cepillado. Cuando esto no sea suficiente, la superficie deberá rectificarse o tratarse con un método de procesamiento mecánico. Con materiales resistentes a la corrosión solo se pueden utilizar cepillos de acero inoxidable; de lo contrario, puede producirse herrumbre por partículas de hierro depositadas en la superficie. Debido a la formación de poros, en el caso del aluminio es importante que no quede en la superficie ninguna película gruesa de óxido. Para limpiar y desengrasar deben emplearse los disolventes adecuados. Atención: si se utilizan disolventes con cloro, pueden producirse vapores tóxicos.
Encendido del arco voltaico
El arco voltaico nunca debe encenderse fuera del arco-aire del material base, sino siempre de manera que el punto de ignición pueda volver a fundirse inmediatamente después de la soldadura. Cuando comienza el proceso de soldadura, el material base del punto de ignición a alta temperatura se enfría con gran rapidez debido a la absorción térmica de las masas frías inversas. El resultado de este enfriamiento rápido puede ser un mayor endurecimiento, en ocasiones incluso con grietas y poros. Este enfriamiento rápido puede evitarse si la ignición se produce directamente al comienzo de la costura de la soldadura y los posibles defectos se vuelven a fundir inmediatamente. El lift arc debe ser una excepción si la máquina de soldadura antes empleada no dispone de sustancia de ignición (ignición de impulsos de alta tensión). En este caso, la ignición se producirá en una plaquita de cobre colocada en el arco-aire, cerca del inicio de la costura de soldadura. Desde aquí, el arco voltaico se desplazará hasta el inicio previsto de la costura y comenzará la soldadura. En el caso de lift arc directamente en el material base, el tungsteno puede entrar en el material de soldadura que no se funde debido a su elevado punto de fusión y, más adelante, detectarse como un punto brillante en la película de irradiación debido a la mayor absorción de rayos X por tungsteno.
Guía de la antorcha TIG
(ver ilustración a la derecha)
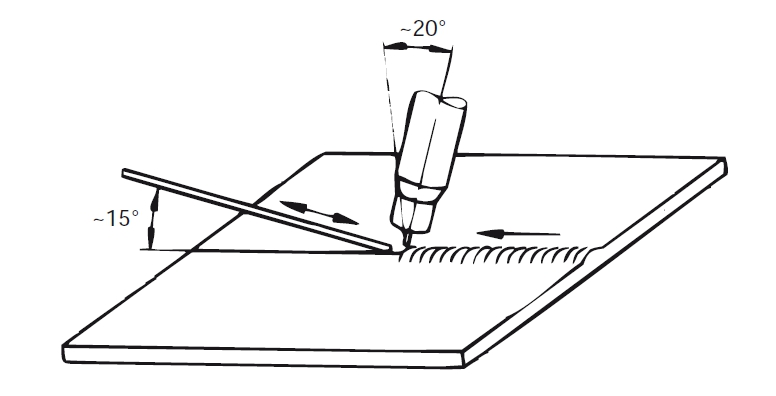
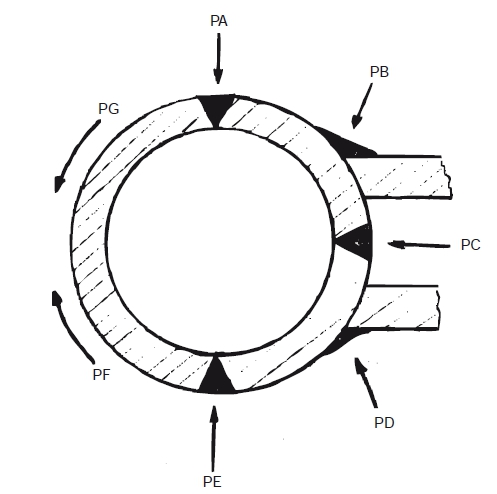
Posición de soldadura
Según UNE-EN ISO 6947, las posiciones de soldadura se designan con PA–PG. Si se observan desde la parte superior de una tubería (PA), se disponen en el sentido de las agujas del reloj en orden alfabético. En Alemania, la posición PA se conocía antes como horizontal o plana. A continuación, siguen las posiciones de soldadura a tope PC (horizontal en pared vertical) y PE (sobre cabeza), así como las posiciones de soldadura en ángulo PB (horizontal) y PD (horizontal/sobre cabeza). Cuando se sueldan chapas, PF significa que se suelda en vertical ascendente y PG es la soldadura vertical descendente. No obstante, aquí se combinan distintas posiciones. La posición PF se aplica cuando la tubería se suelda desde la posición sobre cabeza, sin girar a ningún lado. La posición PG se aplica para soldar de arriba abajo (soldadura vertical descendente). La soldadura TIG es posible en cualquier posición. Como en otros procesos de soldadura, los datos de soldadura deben coincidir con la posición.
Parámetros de soldadura
El límite inferior de la aplicación del proceso TIG es de unos 0,3 mm para el acero y 0,5 mm para el aluminio y el cobre. Hacia arriba, se establecen límites económicos para la aplicación. El rendimiento de fusión del proceso no es muy alto. Por eso, a menudo se sueldan TIG únicamente las pasadas de raíz, mientras que para las capas restantes se utilizan otros procesos (E, MAG) de mayor potencia. Cuando se seleccionan los parámetros de soldadura, se debe tener en cuenta que en la máquina de soldadura solo se ajusta la intensidad de corriente; la tensión del arco voltaico se deduce a partir de la longitud del arco voltaico que guarda el soldador. Por consiguiente, cuanto mayor sea la longitud del arco, mayor será la tensión. Como valor de referencia para una intensidad de corriente suficiente para soldar acero con corriente continua (polos) se utilizará un valor de 45 amperios por mm de grosor de pared. Para soldar aluminio con corriente alterna se necesitan 40 A/mm.
Soldadura con impulsos eléctricos
Cuando se suelda con impulsos eléctricos, la intensidad de corriente y la tensión cambian constantemente entre un valor básico bajo y un valor de impulso más alto, manteniendo el ritmo de la frecuencia de impulsos. Por el efecto de la corriente de impulsos elevada, se produce la penetración en el material base y se forma un baño de soldadura puntiforme. Este comienza a solidificarse desde el borde debido al impacto de la corriente básica más baja, hasta que el siguiente impulso eléctrico vuelva a fundirlo y aumentarlo. Entretanto, el arco voltaico ya se ha propagado a la velocidad de soldadura de modo que la costura de soldadura, en la soldadura de arco pulsado TIG, se forma a partir de muchos puntos solapados. El tamaño medio del baño de soldadura es más pequeño que en la soldadura con corriente uniforme, de modo que puede controlarse mejor en posiciones fijas. No obstante, se garantiza que la penetración es suficiente. El efecto antes mencionado solo se produce si hay una diferencia de temperatura suficiente en el baño de soldadura entre las fases básica y de impulso. Esto solo ocurre con frecuencias de impulsos inferiores a unos 5 Hz. Una desventaja es que, a menudo, la velocidad de soldadura debe reducirse durante la soldadura de arco pulsado. El soldador percibe los impulsos con rango de frecuencia bajo como molestos destellos del arco voltaico. Por consiguiente, esta variante de soldadura TIG se usa menos en soldaduras manuales, en las que el soldador tiene otras posibilidades para controlar el baño, que en la soldadura TIG mecanizada.
Para una buena soldadura TIG se necesita el siguiente equipamiento:
- Fuente de corriente de soldadura
- Antorcha
- Borne de la pieza de trabajo, pinza de masa
- Electrodo recubierto
- Herramientas de soldadura
- Ropa de trabajo de seguridad
Encontrará más información sobre soldadura TIG en nuestro Glosario de soldadura.