MIG/MAG WELDING PROCESSES
forceArc puls XQ
forceArc puls® is a MIG/MAG welding process with a heat-minimised pulsed arc. Easy to handle and suitable for welding non-, low- and high-alloy materials throughout the entire power range.
It is characterised by outstanding gap bridging, even in the high output range and enables controlled welding with an air gap that fluctuates by up to 4 mm.
forceArc puls® – for the best steel and stainless-steel welding of all time with unbelievable cost reductions!
forceArc puls
Advantages:
Faster welding speed- Symmetrical seam formation and the greatest possible seam thickness (throat thickness) on fillet welds.
- Outstanding wetting
- Deeper, more concentrated penetration with reliable root fusion
- Finishing work minimised
- Even for panels with scaling or very impure surfaces
- Minimal stress for the welder while working
- Fewer welding fumes
- Pleasant, quiet arc sound
- Easy to guide (excellent wetting)
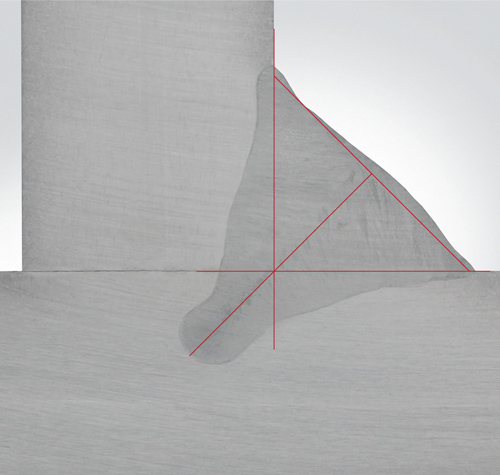
*compared to pulsed arc
Video
forceArc puls
Efficient and cost-effective welding
Welding of stainless steel
The forceArc puls welding process® has up to 15 % lower heat input in the upper power range compared to pulse. This results in less discolouration and less distortion in the component.
Other advantages:
- Minimised energy per unit length
- Reduces distortion, discolouration and tension
- Less finishing work (straightening, sanding, cleaning)
- Less melting loss of alloy elements, producing greater corrosion resistance
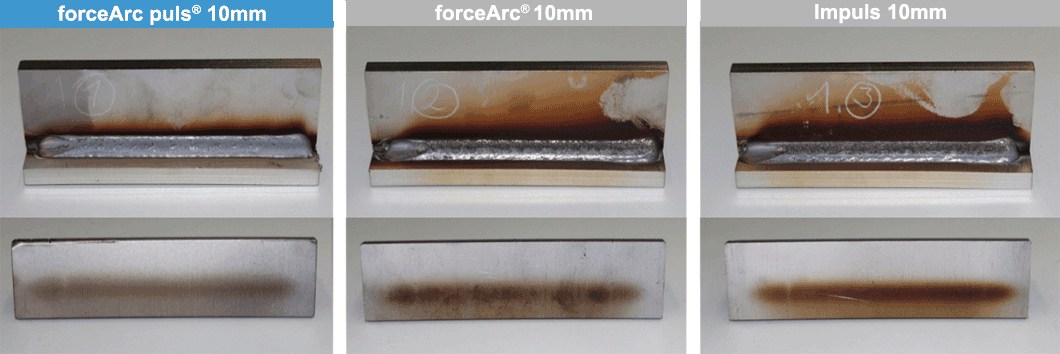
forceArc puls® forms a symmetrical fillet weld. This is the requirement for achieving the maximum throat thickness for a given deposition rate. Up to 20 % greater throat thickness possible compared to pulsed arc.
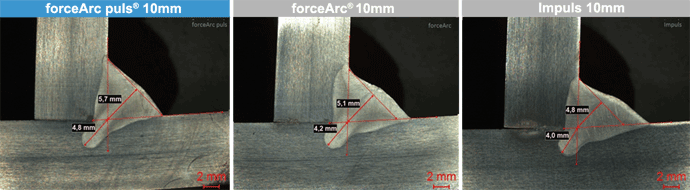
Looking at things from a different perspective, this means welding speeds up to 20 % faster can be achieved compared to a pulsed arc process with an identical throat thickness.
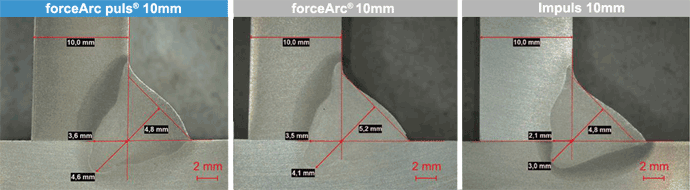
Welding of steel
Your benefits:
- Virtually spatter-free
- Excellent seam appearance
- Few undercuts, optimum wetting on edges
- Insensitive to contaminated and scaled surfaces
- Symmetric weld seam
forceArc XQ
forceArc ® Efficient and cost-effective welding
Heat-reduced, directionally stable and powerful arc with deep penetration for the higher performance range. Unalloyed, low-alloy and high-alloy steels as well as high tensile fine-grained steels.
forceArc
Advantages:
- Smaller included angle due to deep penetration and directionally stable arc
- Fewer passes
- Less distortion thanks to heat-reduced, concentrated arc
- Excellent root and sidewall fusion
- Perfect welding even with very long stick-outs
- Reduced undercuts
- Virtually spatter-free
- Particularly advantageous for dynamic fillet welds, for example
- Components under load, like weight-bearing parts of bridges
- Wagon building and steel construction
- Unalloyed, low-alloy and high-alloy steels and high-tensile fine-grained steels
- Manual and automated applications
- Welded fillet welds exhibit deeper penetration
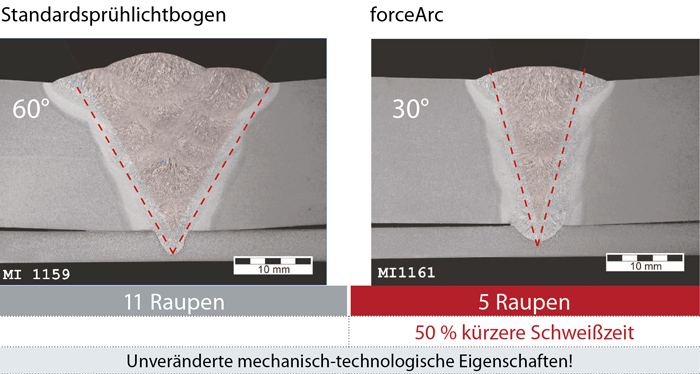
forceArc / forceArc puls
- Combination of forceArc puls, forceArc and coldArc
- Root pass with coldArc, intermediate passes with forceArc and final passes with forceArc puls
- Saves a welding pass with a smaller included angle
- Perfect ignition and crater fill time with forceArc puls, welding with forceArc
- Less material distortion due to reduced heat input
- Lower intermediate pass temperature and minimised joint modification
- Particularly advantageous e.g. when welding fine-grained steels
- Angular shrinkage reduced in fillet welds
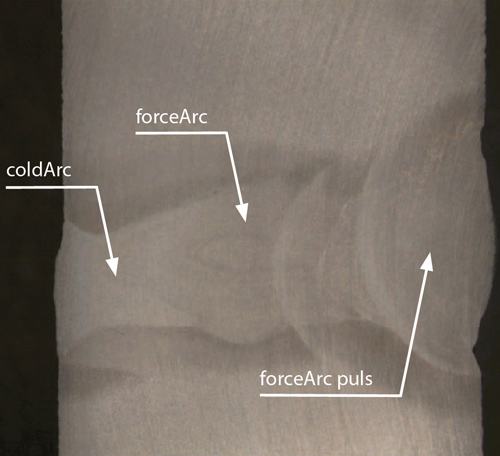
Sheet metal: S 235; 20 mm
Gas: M21 - ArC - 18
Wire: 1.2 mm G4Si1
Runs: 4
Position: PC
Preparation angle: 10°
Welded on one side, without backing bar
Combination of coldArc, forceArc, and forceArc puls
Efficient and cost-effective welding
- Overall cost savings of up to 60 %
- Minimal seam preparation
- Fewer passes
- Less welding consumables and shielding gas consumption
- Faster welding time
- Particularly advantageous with dynamically loaded components
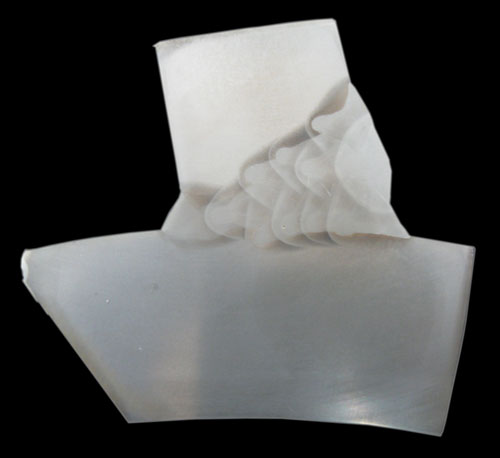
Sheet metal: S 355; 30 mm
Gas: M21 - ArC - 18
Wire: 1.2 mm G4Si1
Runs: 11
Position: PB / PA
Preparation angle: 25°
Welded on one side, without weld pool backing with forceArc
rootArc XQ / rootArc puls XQ
The arc with optimum control of the weld pool
Effortless gap bridging in the vertical-down weld
- Stable, firm vertical-down weld without any inclusions of the molten metal
- Very good gap bridging
- Heat-reduced, low-spatter arc
- Superb root formation and secure sidewall fusion
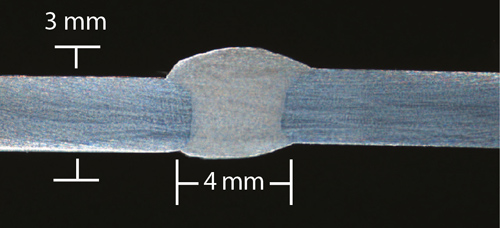
rootArc / rootArc puls
- Heat input, if necessary, with rootArc puls
- Root welding with rootArc: Effortless controlling of the weld pool
- Pass build-up and final passes with rootArc puls
- Performance enhancement for thick metal sheets with rootArc puls
- Switch between rootArc and rootArc puls by pressing the torch trigger for secure overlaying of tack points
- Effortless mastery of the weld pool by changing between rootArc and rootArc puls when superPuls switched on
- Quick and easy welding of vertical-up welds by changing between rootArc and rootArc puls when superPuls switched on
Vertical-up welds in the PF position
- Excellent welding in vertical-up weld positions (PF) with rootArc superPuls
- Secure formation of the root base
- Weaving no longer required
- Smooth bead ripples result in aesthetically pleasing weld seams
Your benefits
- Reliable short arc welding in all positions
- Ideally suited for vertical-up welds (PF) without using the laborious "Christmas tree technique"
- Quick and reliable root welding in TIG quality
- Effortless welding of vertical-up/down welds and overhead welds
- Ideal for CO2 and mixed gas
- Reduced-energy short arc for effortless mastery of gaps
- Low-spatter, digitally-controlled material transfer
- Perfect for sheet metal from 1 mm and greater
- Excellent for butt welds and lap welds
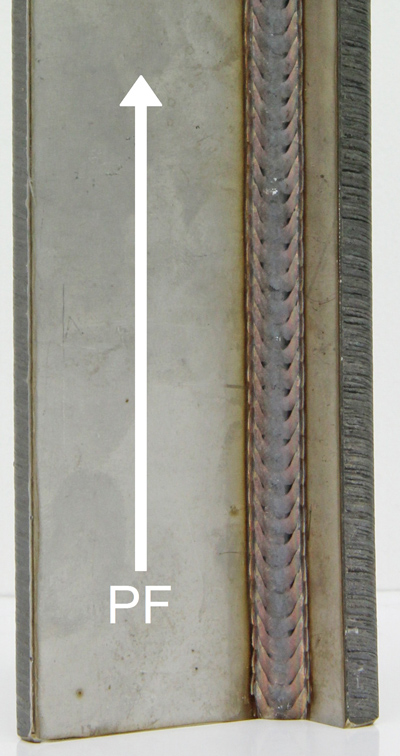
wiredArc/wiredArc puls
Welding with constant penetration
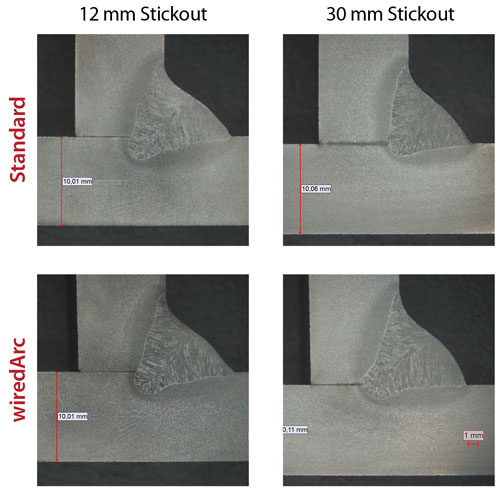
wiredArc/wiredArc puls
Welding with constant penetration
With EWM wiredArc, the penetration remains consistent when the stick-out is changed. The innovative control adjusts the wire feed speed and keeps the welding current and voltage consistent for an even heat input.
- Constant welding current thanks to digital process control
- The energy per unit length and heat input remain virtually consistent despite changes to the stick-out
- Consistently high penetration depth, independent of change to the stick-out
- Ability to reduce the seam's included angle and therefore the weld seam volume
Video
wiredArc / wiredArc puls
Welding with constant penetration
Positionweld
Easy, safe positional welding
Positionweld
Combined process variant for the welding of unalloyed to high-alloyed steel and aluminium alloys for positional welding
- Straightforward handling
- Reliable root fusion
- The “Christmas tree" technique is no longer required for vertical-up welding
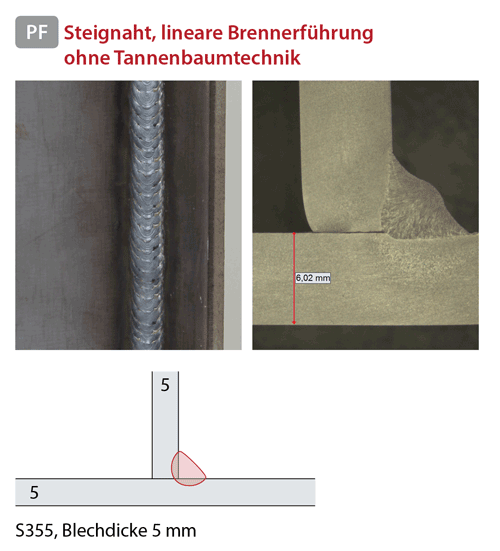
Video
YouTube video
EWM welding process: Positionweld
coldArc / coldArc puls
Perfect welding and brazing
coldArc / coldArc puls
coldArc:
Heat-reduced, low-spatter short arc for high dimensional stability welding and brazing, plus root welding with excellent gap bridging capabilities.coldArc puls:
The optimum enhancement for the higher power range, with focused heat input exactly where the heat is required.- Less distortion and reduced discolouration thanks to minimised heat input
- Considerably reduced spatter thanks to virtually power-free material transfer
- Impressive process stability even with long hose packages without additional sensor leads
- Commercial torch systems, as the material is transferred without drive in the torch, causing no wear and tear
- Easy welding of root passes in all panel thicknesses and in all positions
- Perfect gap bridging even with inconsistent gap widths
- Excellent wetting of surfaces when brazing thin metal sheets
- Minimal finishing work, ideal for visible seams thanks to low-spatter process
- Unalloyed, low-alloy and high-alloy steels and also dissimilar joints of even the thinnest metal sheets
- Brazing of CrNi sheets with CuAI8/AIBz8
- Brazing and welding of coated metal sheets, e.g. CuSi, AlSi and Zn
- Root welding of non-alloyed and low-alloy steels and high-tensile fine-grained steels
- Visible CrNi seams within the thin metal sheet range
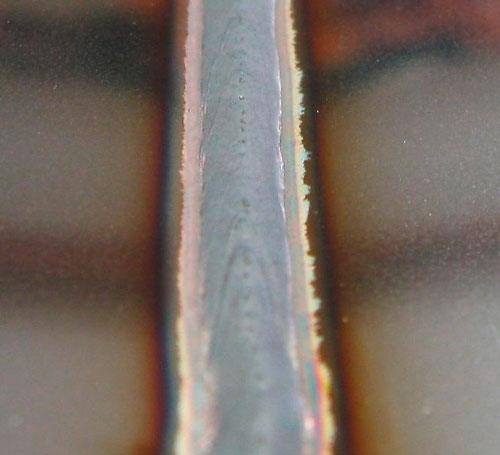
coldArc / coldArc puls
- Heat, where heat is needed, with coldArc puls
- Root welding with coldArc: full control of droplet transfer, minimised risk of lack of fusion
- Pass build-up and final passes with coldArc puls
- Performance enhancement for thick metal sheets with coldArc puls
- Perfect welding with transitional areas with coldArc puls
- Press torch trigger to switch between coldArc and coldArc puls for secure overlaying of tack points.
- Turn on superPuls to switch between coldArc and coldArc puls automatically for straightforward modelling of the molten metal.
- When superPuls is turned on, the machine switches automatically between coldArc and coldArc puls for outstanding and straightforward welding in the vertical up position, without using the "Christmas tree technique".
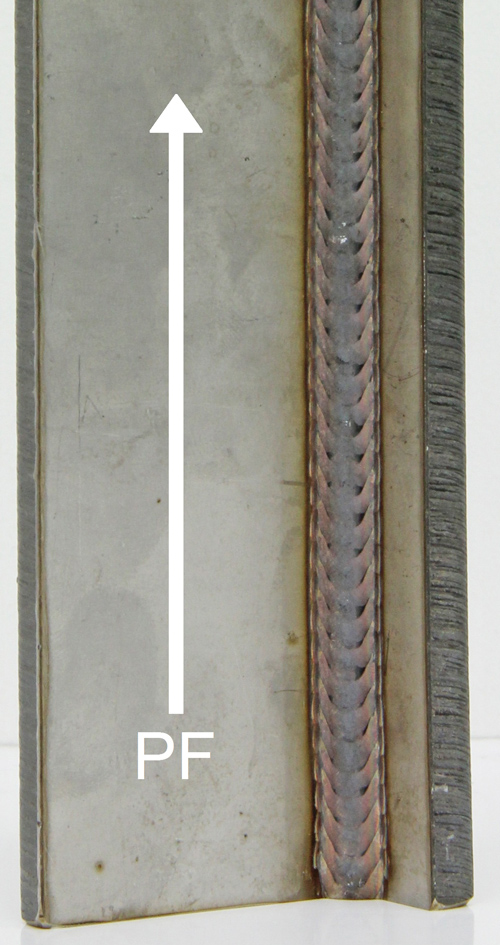
Unique gap bridging for root passes
- coldArc delivers perfect gap bridging, even with alternating gap widths
- No sagging of the molten metal
- Secure sidewall fusion even with misaligned edges
- Total elimination of "wire stab"
- Root passes for all material thicknesses in all positions
- Pass build-up and final passes with coldArc puls