TIG WELDING PROCESSES
activArc
Dynamic TIG arc with compensated arc performance
activArc
Advantages:
- Dynamic TIG arc for targeted and concentrated heat input
- Safe TIG welding in all positions and panel thicknesses
- Full control over the arc energy
- Influence over the viscosity of the weld pool
- Noticeable concentration of energy and increasing arc force as the arc becomes shorter
- Prevents mistakes while tack welding – tungsten electrode does not stick if it lightly touches the weld pool
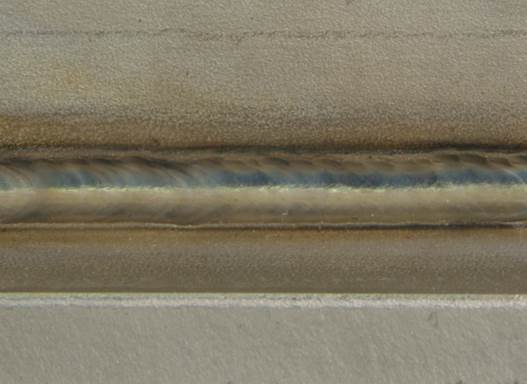
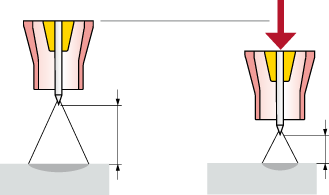
Large distance, approx. 12 V welding current 60 A |
Short distance, approx. 10.5 V welding current 60 A |
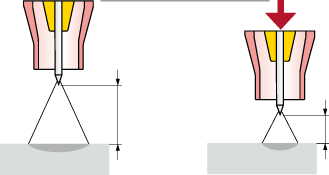
Large distance, approx. 12 V welding current 60 A |
Short distance, approx. 10.5 V welding current 68,5 A |
activArc
Welding made easier
Reducing the distance between the tungsten electrode and the workpiece during welding permits concentration of the arc with constant arc energy.
Changing the arc length changes the voltage, which results in output fluctuations in the arc.
With activArc, output fluctuations are counteracted as the arc length changes. When the arc is shortened, the welding current is increased; when the arc is extended, the welding current is reduced.
Advantages
High cost savings:
- Weld quickly with the focused arc
- Less finishing work by reducing discolouration on the workpiece
- Better root fusion
- Deep penetration
- Concentrated heat input
High quality welding results:
- Minimisation of errors when tack welding – avoidance of tungsten inclusions
- Minimal material distortion
- Improved TIG arc stability, particularly with low current.
- activArc properties adjustable for every material thickness
Benefits in combination with metallurgical pulsing:
- Precise, focused arc with even greater energy density
- Higher plasma pressure of the arc
- Faster welding during manual and automated solutions
- Reliable, uniform penetration
- Reduced heat-affected zones
- Arc length changes have hardly any negative influence on the welding results - particularly during manual welding - constant arc energy
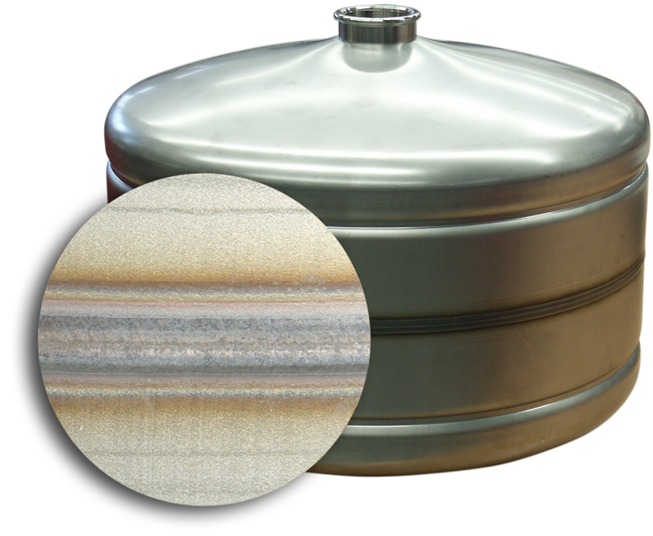
tigSpeed
TIG hot and cold wire welding
dynamic wire feed system
The continuous wire feeding is superimposed by backwards/forwards motion of the wire. The welding process is especially stable with a simultaneously high deposition rate. The tigSpeed systems are available in cold wire and hot wire versions with both manual and automated operation.
Video
tigSpeed
TIG hot and cold wire welding
dynamic wire feed system
tigSpeed
Advantages:
- Perfectly controllable weld pool, even with positional welding, such as vertical-up position
- Extremely high welding speeds – similar to MIG/MAG welding, but with low emissions and no spatter
- Reduced heat input, minimised distortion, less shrinkage of workpieces, and optimised impact work-values
- Reduces welder fatigue thanks to easier handling and more comfortable working positions
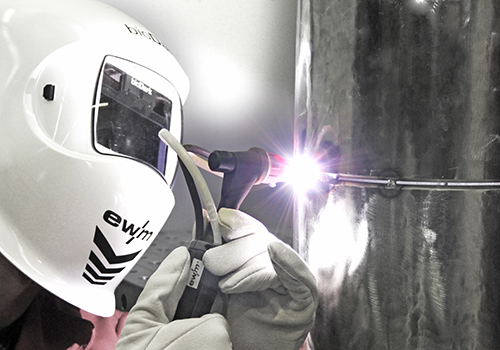
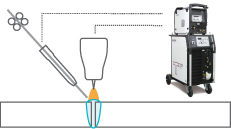
Hot and cold wire welding:
- Up to 60 % higher deposition rates*
- Higher seam quality* thanks to significantly reduced dilution when surfacing
- Reduces welder fatigue thanks to easier handling and more comfortable working positions
* Compared to manual TIG welding
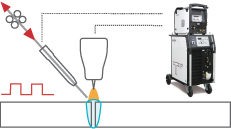
tigSpeed: forward/backward motion of the wire:
- Ideal for positional welding
- Perfectly controllable weld pool through superimposed forward/backward motion of the wire
- Optimum seam appearance with shapeable bead ripples thanks to infinitely adjustable frequency of the forward/backward motion of the wire
- Reliable welding of root passes at high welding speed
tigSpeed
Welding speed comparison
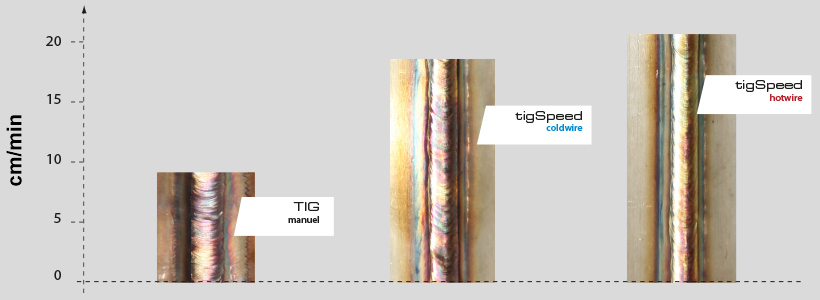
Up to 14 m radius of action:
- Flexible thanks to individually adjustable hose package lengths
- Optional trolley for increased mobility
- Optimum protection of the intermediate hose packages through strain relief
- Areas of application: low-, medium- and high-alloy materials; CrNi; nickel-based alloys, copper and copper alloys; aluminium and aluminium alloys; special metals P91/P92
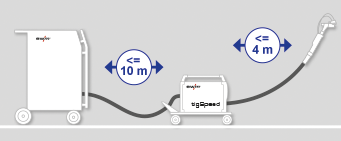
Additional product information and technical data on the tigSpeed system is available here:
tigSpeed oscillation drive 45 coldwire
tigSpeed oscillation drive 45 hotwire
tigSpeed continuous drive 45 coldwire
tigSpeed continuous drive 45 hotwire
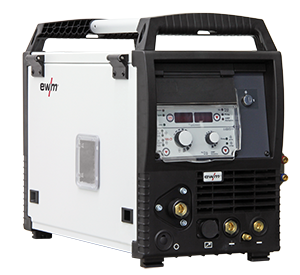
spotArc
TIG spotArc® spot welding
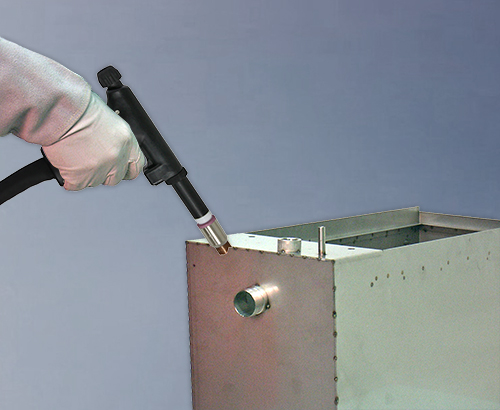
Perfect surface formation:
- Flatter spot formation in comparison to MAG spot welding
- Exceptional spot connection characteristics thanks to minimal heat input
- Very low thermal stresses and little distortion due to short welding times
- Perfect for visible joints due to clean seam appearance
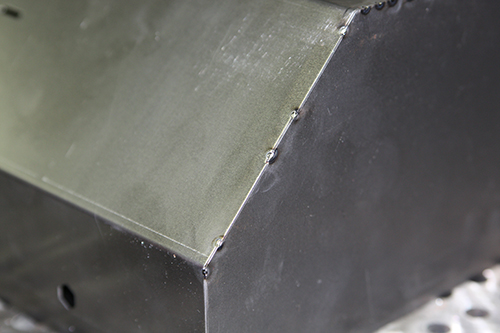
The right nozzle shape for every application
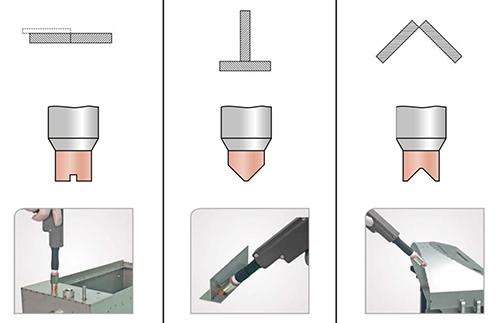
forceTig
TIG welding process with a highly focussed arc for greater penetration and faster welding speeds. With its forceTig welding process EWM enters new fields of TIG welding. This joining process enables a much higher energy density in the weld pool by way of an extremely concentrated welding arc and makes possible the fastest welding speeds.
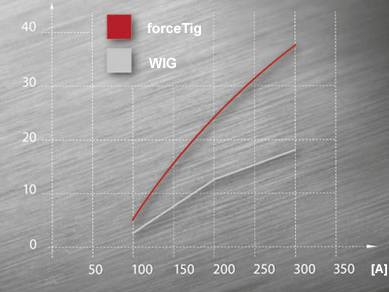
Comparison of arc force TIG / forceTig
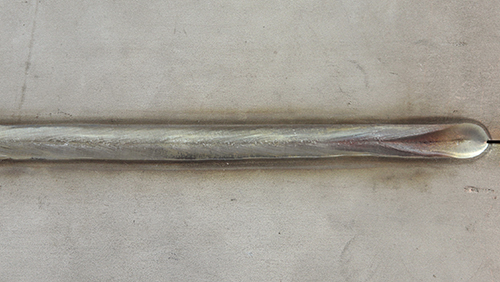
forceTig
Advantages:
- Less energy per unit length thanks to the strongly focussed TIG arc with high energy density at a higher welding speed
- Single-pass welding of thin and thick metal sheets is possible
- For fully mechanised and automated manufacturing processes
- 100% reproducible TCP, perfect for automated applications
- High torch power: 800 A at 100 % DC
- Electrode easy to change without gauges thanks to defined, calibrated geometry
- Very high current-carrying capacity, high current density
- Stable welding torch design for increased crash safety
- Highly effective closed cooling circuit
- Low procurement costs and energy requirement
- Cold/hot wire applications
Video
Youtube-Video
EWM WELDING PROCESSES: forceTig